Six Sigma and Lean in Technology Development | Technology development is the fuel that powers the timely delivery of new products and production processes. It enables the fulfillment of product portfolio requirements and growth goals of the business. At PDSS, we consider technology development to be a strategic process that is heavily influenced by the product portfolio renewal process. Product commercialization is a tactical process that is fed by these two strategic processes.
Product portfolio renewal activates a product commercialization project, while technology development transfers robust and tunable technologies that enable product commercialization projects. We take the position that the best and earliest opportunity to develop a product's Six Sigma performance is during technology development; it is the starting point for the physical development of quality and efficient cycle-time in product commercialization. Six Sigma in technology development prevents downstream problems.
A Six Sigma technology development project delivers a complete, integrated entity ready to be transferred to a product commercialization project. While not easy to do, technology development projects should be largely independent from product commercialization projects to minimize technical difficulties and schedule delays. It is risky to develop new technology within a product commercialization project. There is a big difference between what needs to be done and known during technology development vs. product commercialization. Technologies that are under development are immature and overly sensitive to sources of noise in the form of variability in manufacturing, distribution and customer use. When they are prematurely forced into the high-pressure timeline of a commercialization project, corners get cut and sensitivities to variation go undetected. Immature, underdeveloped technologies can slow the progress of the product due to their inability to integrate smoothly and function correctly in the presence of noise factors, or any variation from external unit-to-unit, or deterioration sources. In a word, they are not "certified" for safe commercial or design application. Deploying new technologies before their certification is analogous to launching a new product design that has not been made capable from a manufacturing, assembly and serviceability perspective. To the statistician, it is similar to running a process before one has proven it to be under a state of statistical control.
New technology should be quantitatively proven to be both robust and tunable before it can be used in a new product. By "robust," we mean capable short-term performance as measured by Cp indexes, even in the presence of noise factors. By "tunable," we mean capable long-term performance as measured by Cpk indexes. (for more about the capability indexes "Cp" and "Cpk", see second article, below).
Technology development and transfer must be properly controlled and managed by facts generated using a system integration process called Critical Parameter Management (CPM). CPM has been the subject of several previous newsletters (see 2008-Jul, 2008-Aug, 2010-Jan, 2010-Mar) and is extensively explained in the text Design for Six Sigma in Technology & Product Development by PDSS President, Skip Creveling and Slutsky & Antis.
CPM should be initiated during advanced product planning and technology development. If done so, then a certified portfolio of critical functional parameters and responses can be rapidly transferred as a "platform" in the design of families of products.
CPM is a system engineering and integration process that is used within an overarching technology development and product commercialization roadmap. These roadmaps can be stated in terms of manageable phases and gates to enable product development with order, discipline and structure. The phases of PDSS' generic roadmap for technology development, whose acronym is I2DOV, are Invent & Innovate, Develop, Optimize and Verify.
Chapter 5 in Six Sigma for Technical Processes by Skip Creveling describes how the process of technology development should properly develop and transfer new technologies to a product commercialization project. Some people may not consider Six Sigma and Lean appropriate for research and/or technology development. PDSS, however, believes the goal of the technology development process is to transfer robust and tunable technologies that are desensitized to strong sources of variability (Six Sigma) by using customer-oriented, valued-added workflows (Lean). |
Cp, Cpk and Process Capability Analysis |
Treasure Chest of 6Sigma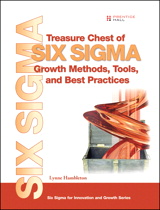 | From Treasure Chest of 6 Sigma Growth Methods, Tools and Best Practices by Lynne Hambleton, one of our colleagues and consultants at PDSS. This topic is presented on pages 486 - 515. The following is an excerpt:
Process Capability Indexes (CPI's) statistically quantify the ability of a process to produce output that meets customer requirements by calculating variability differently, depending on the duration of the data (short- or long-term). While there are several CPI's available, the most commonly used indexes are Cp and Cpk.
Cp is the Specification Spread (USL-LSL) divided by Process Spread (6s), where USL = Upper Specification Limit, LSL = Lower Specification Limit and s=Standard deviation for a sample, or an estimated standard deviation.
Cpk is the difference between the Closest Specification Limit to the Process Mean (x-bar) divided by half of the Process Spread (3s), where x-bar is the sample mean. The value of Cpk is the smaller of these two calculations: (USL - x-bar) / 3s and (x-bar - LSL) / 3s.
Cpk is the most popular calculation of process capability because it considers both variability and mean of process output relative to customer requirements.
Cp can be considered the "upper bounds" of Cpk when the process mean is on target. The difference between Cp and Cpk represents the potential gain in process capability if the process were to be centered.
Rules of Thumb: Cp should ideally by greater than 1.5 to be capable. Some experts accept a process with Cp greater than 1, however, that is the bare minimum. The larger the Cp, the better.
Cpk should be greater than 1.33. For a Six Sigma process, Cpk = 2.0.
|
Is there a topic you'd like us to write about? Have a question? We appreciate your feedback and suggestions! Simply "reply-to" this email. Thank you!
Sincerely, | |
Carol Biesemeyer
Business Manager and Newsletter Editor Product Development Systems & Solutions Inc. |
|