
Still April right? Barely, but at least I am on schedule for this month's tip...thanks to Anne of course!
It is ramping up to be a very busy summer and I am sure most of you can say the same. But when does our world really hit an absolute slow time?
Be sure to check our website for some newly added downloadable resources. When discussing upcoming conferences last month, I left an important one off and that is NFMT's High Performance Buildings & Workplaces on May 3 & 4, 2016 in Austin, TX. Geez, that is only 6 days away so check it out and be sure to register to attend.
Til next time.
 |
 All too many maintenance and facility managers feel Capital Planning is something which is more of a pain in the back side than it is a benefit to the organization. Or at the very least is something the finance or administrative office should be responsible for, not the maintenance managers. Many maintenance managers also feel that they will only have to give up money when it smokes and burns or dies completely; why ask two years before it happens? The Reality - Maintenance or facility managers are the perfect people to be in charge of the capital budget. Who else in the organization knows what the operating status, condition, and expected life of your assets and equipment really is except the employees that operate and maintain your equipment and buildings each and every day.
Capital budgets can be called by many names, investment appraisal, capital budgeting, life cycle budgeting, and capital improvement programs (CIP), to name a few. The bottom-line, it does not matter what you call it; it is an organized process to keep track of all or your company's assets, the condition of the assets, and your estimate of when that asset or system will need to be replaced.
To develop a good and well-functioning capital system you need several key components.
- A complete list of all assets and equipment within your fence line. Without this you will never have a complete understanding of your replacement and capital needs. This list must be organized by:
- building
- department section
- system
- asset, etc.
- An estimate of the expected life of the items listed.
- The estimated of what the replacement cost will be at the time of replacement including all demolition and re-installation costs.
- The last item needed is the priority of the asset. How important is this item in relation to all other assets and equipment on your list?
I recommend the first time you attempt to develop your capital list you begin by "blue skiing" all the possible items you would like to replace or purchase for the first time. Prioritize this list and it will quickly show you which ones are simply a 'wish list' and which ones are truly important to maintaining your business operation and structure. Having this detailed information allows your management team to do two things,
- Maintain all assets and systems in a like-new condition, and
- Financially plan the company's cash flow and financial planning as it relates to interest rates and lines of credit which most companies use to manage the capital investment side of the business. One of the keys to a successful business is to be able to properly plan and forecast all major capital expenditures. In simple terms, never have any financial surprises during the year.
This may sound like a lot of work but it really is not; considering that you already have (or should have) a computerized maintenance management system (CMMS). If you have it properly installed and populated then you will already have your detailed equipment list with all of the information needed to begin developing your capital budget list. If it is properly populated then you have what I call the birth certificate information on all of your assets.
- Date purchased
- Cost of the purchase
- Name and serial number
- Capacity, horse power, voltage, pressures, CFM, etc.
- Who you purchased it from
And, if you are properly writing work orders for all of the individual repairs and problems you now have a great source of the condition and estimated life of the piece of equipment. You are three quarters of the way there to developing a great capital budget. Keep in mind when you begin developing your 'wish list' to involve as many people as is practical. This would include all of your maintenance technicians, contractors, and vendors that have worked on the equipment and even some of your customers as appropriate. Don't forget you can always delete the item from the list if it doesn't rise to the priority which will place it on next year's final list. In time it will rise to the level where it needs to be replaced and you will have all the information needed to quickly add it.
Once you have your list complete and the financial component is approved you need to ensure the expenditure and installations are completed in a timely fashion. I would have monthly meetings to ensure you stay on top of the process. Nothing upsets upper management more than to have money approved to replace equipment and assets and half the year goes by and nothing is done. They begin to wonder why they approved the funds if no one is going to spend it. They begin think, "I wonder if they really needed that in the first place." Bottom-line, spend it and spend it quickly before it gets withdrawn.
Final Thoughts
- Identify and name all of your assets and equipment
- Maintain your work order and asset history
- Great source of information and history
- Maintain a long range capital "wish list"
- Manage your capital replacement program with discipline and accountability
Last month I presented a Capital Planning 101 session at the NFMT-Baltimore conference. If you would like a copy of the presentation please use this link provided or ( Presentation) contact Anne and she will send you a copy.
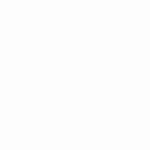
|
May Tip of the Month
Maintenance Quality Control
|