Here are some ideas around how to reduce some of those computerized maintenance management system (CMMS) headaches you've experiencing from time to time. Unfortunately, there is a popular misconception that having a CMMS will solve many of your facility maintenance problems. A belief mostly held by non-maintenance professionals, sorry there are no "Silver Bullets." Everything in our lives now involves a computer in some way or another. I recently purchased a new pick-up truck and I can unlock it, start it, roll down all the windows from anywhere in the world. I guess that sounds pretty cool to some but I am trying to figure out how I am going to use it. I guess I could install that on my wife's car and every now and then roll the windows down while she is driving - that might be fun once or twice - although I doubt she would see the humor in it.
The point is, computers are everywhere and they will do anything we want them to do and sometimes anything they want to do as well. A CMMS is no different; it will do anything you want it to do. The key is having a process in place and accurate data to 'feed the beast'. CMMS programs are similar to using handhelds for maintenance data recording. They only give you faster access to bad or incomplete information which leads to not being able to make good decisions, hence the development of headaches. Examples of headache causing problems could be:
- Management needs historical data to assist with budgeting capital expenditures - Oops data is incomplete!
- Management is talking about outsourcing your department, time to gather all the data about the wonderful work you and your team have been doing and what it has cost over the past five (5) years - Oh no data is missing.
- Management wants a 10% reduction in your supplies and labor costs. Now you have them right where you want them, you will show them what is going to be dropped or ignored by a reduction in maintenance performance - Oh gee nobody has been writing work orders for specific jobs it just says "Bubba and Skeeter worked eight (8) hours each day last week," and the work description says "stuff broke" and the comment section says "stuff fixed."
So we all have been there, suffered through those meetings with the bosses, and we can't relay what is actual going on but can only give him our thoughts and perceptions, here comes another... Excedrin moment!
The anti-headache medicine is pretty simple; you have to have the answer for all of those annoying questions you have not been able to answer in the past. Think about it like your administrative person does when you go on a business trip. You come back to work and they want an expense report filled out before you get reimbursed. They have lots of questions. What was this $10 for? Why was your dinner $35 when there was a Cracker Barrel next door? Why do you want us to pay for the movies you watched in your room (now we have trouble)? So, the key is to have a system in place that captures all of this type of data for all of your assets and equipment. Here is a short list of what you need to accomplish this.
- Your CMMS must be up and working well with good network speeds.
- Have a process to name all of your systems and assets so you can sort them later as you want and need.
- Populate as many of the fields and blanks as you can with pertinent information. Again, this will prove to be very useful when sorting for reports.
- Write a work order for all work by the job, not the day or week. Work orders for all work (this will take some leadership and discipline) must be demanded.
- Work orders that go out this morning come back this afternoon (leadership and discipline again) no stacks of paper on lockers and dashboards of trucks.
Remember you must have processes in place which are managed with discipline and which have a strong element of accountability built into the audit process.
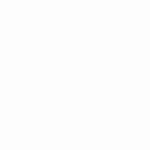
|