Over the past several years equipment and facility risk assessments have been on many managers and owners minds. Risk assessments are relatively simple and easy to accomplish. You can make them quite complex if you choose but those are normally reserved for equipment and systems where the consequences of failure are catastrophic and possibly life threatening. The commercial airline industry comes to mind quickly.
The simplest of all risk assessments begins by asking yourself and your team, what happens if this fails? From the answer to that question you will be able to prepare for the failure and hopefully prevent it from occurring in the first place, or at the very least put in place processes or equipment to reduce the consequences once it does occur.
As you begin the process of developing a risk assessment program you must discuss and decide what your appetite and tolerance is for risk. In other words, do you like taking educated risks or do you like rolling the dice once in a while? Ask yourself the tough questions:
- What will the failure and/or downtime cost the organization?
- How will it affect my business and ultimately my profits?
Now that you have discussed your tolerance for risk you can begin the process. I suggest starting with a relatively simple one like the electrical power to your facility. You want to ask several questions using your facility history as a guide.
- How often do we lose power?
- How long does it normally stay off?
- What are the consequences when these events happen?
If the power is down three (3) times a year and it is only off for four (4) hours and the cost to you is low, then you may decide to do nothing. On the other hand if the cost is high and the outage has long- term ramifications to your business then it would be time to consider some alternate methods of providing back up power like generators.
There are many formalized processes and applications to assist in the assessment process. I recommend you use one of existing documented processes which will create a standard method for the analysis for your entire organization. Most all of the existing processes involve three (3) major components.
- Severity-how severe are the consequences of the failure?
- Occurrence- what is the frequency of the failure event?
- Detection- can you detect the failure before it happens or can you detect it quickly after it begins so as to reduce the severity of the failure?
If you use an organized application or process they often place numerical values on the process components so all equipment and systems can be numerically rated in order of importance or severity which allows you to develop short- and long-term plans for remediation.
Again this can evolve into a very complex process or you can keep it relatively simple. I suggest beginning with a several sessions for you management team and brain storm your critical processes and equipment to determine where to start. Always look at life safety first, then on to compliance issues, and then to the failures that may keep you up at night and very often cost you money and business opportunities.
Here is a link to a recent conference presentation which will give you some more insight and details into risk assessments. It also focuses on one risk assessment process in particular that I have used several times, FMEA. There are several books written on this process if you are interested in learning more about the process.
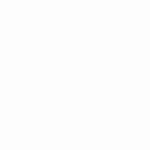
|