 I know many of you are experiencing everything from power outages, ice build-up, and continuous snow. What a headache these last several days (weeks) have been. I certainly hope March brings us all better weather. A quick note for those of you who are planning to attend NFMT-Baltimore in a couple of weeks. I hope you will plan to attend one of my presentations and to visit Anne Copeland and me at our expo booth #1938. This year's conference/expo Conquer Your Toughest FM Challenges brings together some of the best speakers and exhibitors in the business...and you can't beat the cost - Free! I hope you are and will consider attending. See you Next Month!
|
Building a PM Program From Scratch...
or From the Ground Up
|
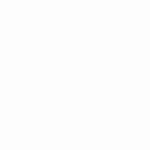
This month's tip can save you thousands of your organizations' money! One of the fundamental components of a well-run maintenance organization is a Preventive Maintenance (PM) program. PM programs are the "Holy Grail" of asset reliability and maintenance. Most organizations have a poor or non-existent PM program in place. Even though we take care of our personal assets like cars and our homes we don't transfer that culture to our work assets. The big question is why? I can honestly say I don't know. It truly baffles me how we take very good care of our personal equipment and vehicles but not transfer that culture to our work place. We don't seem to understand the cost ratio of not maintaining equipment in a like new condition to what it costs us to run it to failure. Like new condition is not the condition of the antique car that is worth $100,000.00 but a condition where the asset runs, performs, and operates like it did when it was new. It may need paint and some dusting but it still operates like it should.
So the title of this month's tip is Building a PM program from Scratch or from the Ground Up. The building the program from scratch came from many who are scratching their head (or some other part of their body) trying to figure out how to develop a good and reliable PM program. So here are the keys to developing a program that will last for years and contribute to your organization over and over.
- Prioritize your assets, equipment and systems. You can't start a PM program without knowing which systems and assets should get the special care and attention first.
- Review all your assets and list them in order of priority. These pieces of equipment should get the preventive maintenance inspections before all other equipment.
- Write very simple and basic checklists that cover the fundamental needs and requirements required to keep the asset or equipment running in a normal or like new condition.
- Remember it doesn't have to look beautiful. The key is that it operates and runs in the manor that serves the original purchased intent.
- Create drive-by or walk-by routes where a technician comes in contact with the asset or equipment on a scheduled and regular basis. Always getting close enough to listen, touch, and look at how the asset or equipment is operating. Basic and simple observations should be noted on the PM work request.
- Remember, every PM inspection should improve the next PM procedure.
- Document everything that is done during the PM procedure or inspection.
- Remember if you document your actions that occurred during each and every inspection you will be able to predict your future. "If you know your the history you can predict your future."
- Fine tune and modify your program. Every time you perform a PM you should be asking yourself if the PM could be performed better and maybe faster.
- Were the hours planned accurate?
- Were the tasks appropriate for the equipment and its expected performance?
- Is the frequency of the PM accurate, should it be adjusted to save time and money?
- Remember you can over PM equipment especially if it is invasive.
- Consider reviewing and revising PMs every time you have an unexpected failure or event. Always ask the question, Why did it fail and how could I have prevented the failure from occurring with improvements in the PM program?
- Keep in mind all failures can be prevented with enough effort and time.
- Audit the PM program. Any program or process should be audited to ensure the process and program is producing the desired results when the program was designed. PM programs are no different. You should be able to measure the success of the program by looking at the following measures:
- Work requests within 30 days of a PM
- Multiple work requests between PM inspections
- Catastrophic events with equipment
- Numerous problems found during a PM inspection
- Percent of PM work requests compared to total maintenance work hours. Should be 50% or more!
The bottom-line is there is no such thing as a bad PM inspection, only better ones. Start your process even if it is simple; only technician walk-by's or drive-by's. At least they are looking, listening, and touching the equipment. Hopefully they are writing work requests for what they see and in time you will begin to improve the performance of all equipment.
Remember, the only way to emerge from a work style of reactive and emergency work is to have a well run preventive maintenance program. Don't make it too difficult, just do it!
See You Next Month!
|
March Tip of the Month
Are You a Reactive or a Pro-Active Manager? or (Are Your Managers Reactive or Pro-Active?)
|
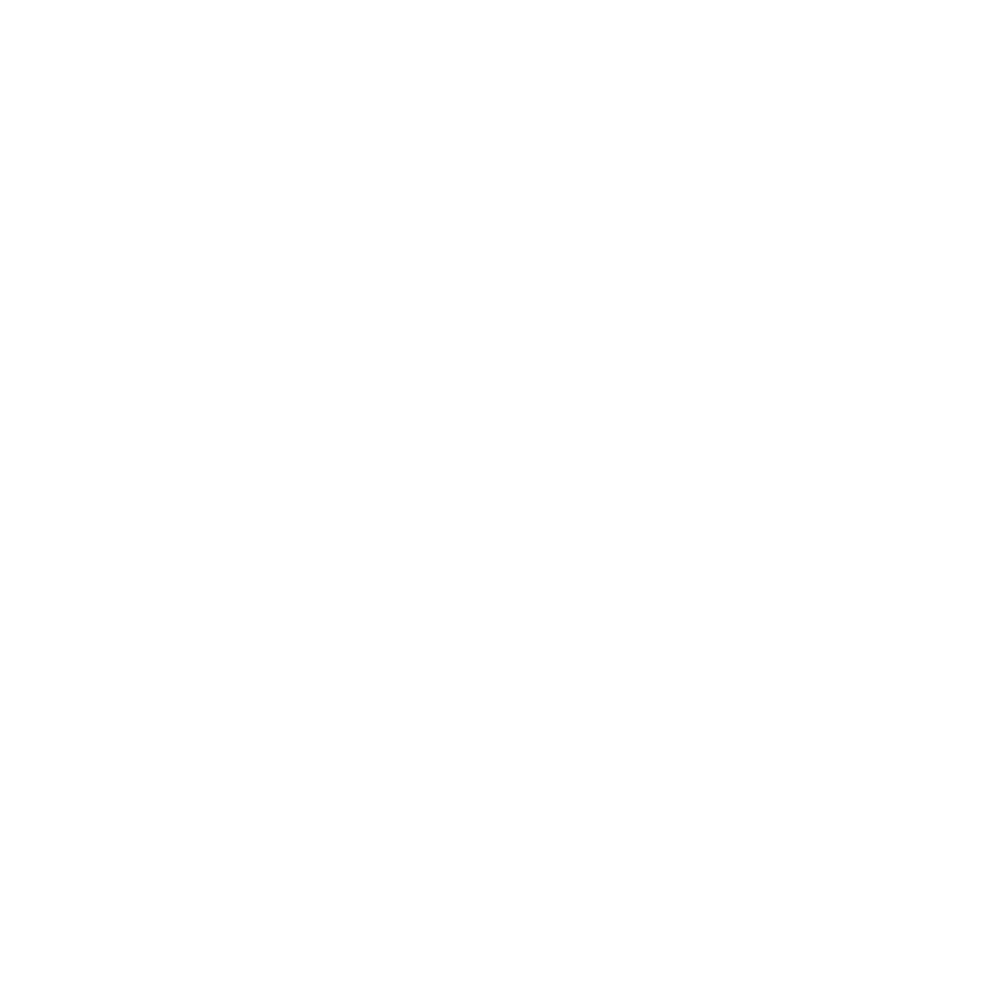 |
Miss an Earlier Tip? You will find them all here MN&B Issues
|
|
|
|
Benefits of Planning & Scheduling Mike discusses the benefits of planning and scheduling Video Link
|
|
|
|
| 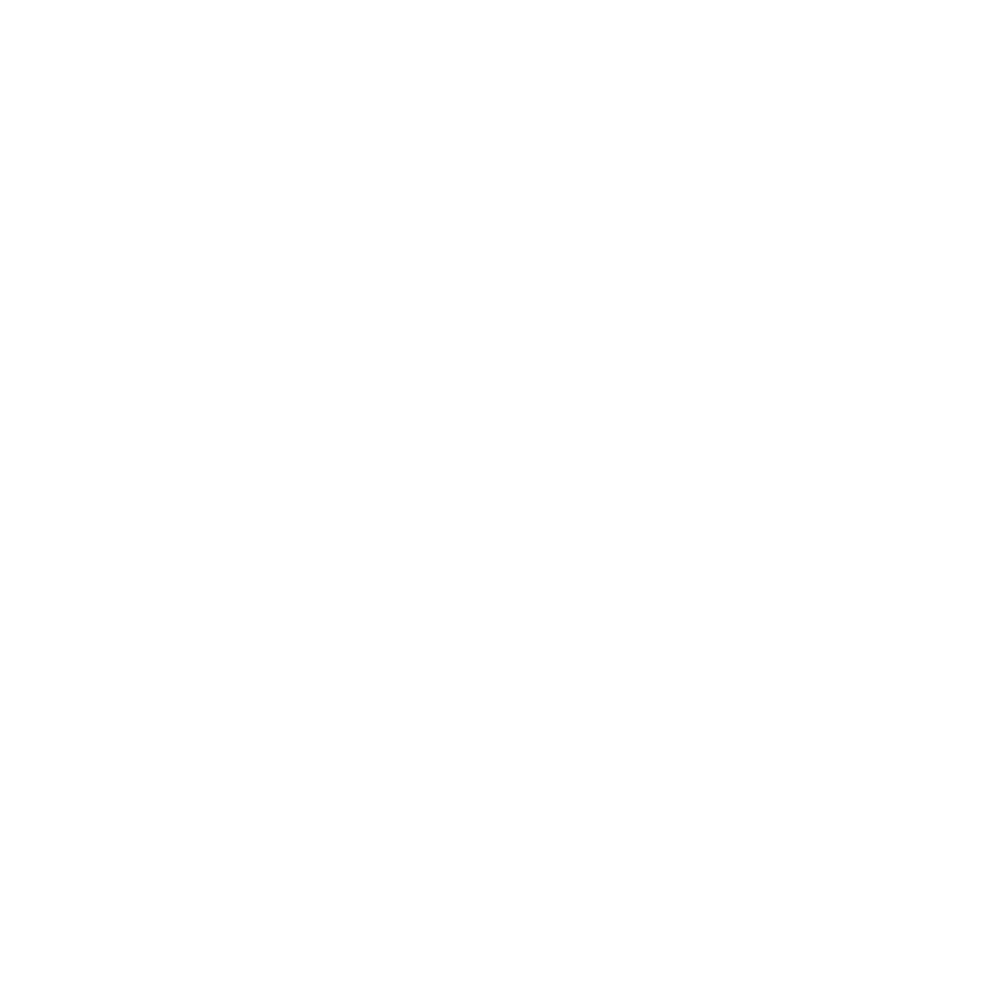 |