Welcome new members
Flexible Assembly Systems Inc
San Diego, CA United States
Hexagon Engineering Lagos, LA Nigeria
RF Automatizacion Tibas, San Jose Costa Rica
The Oilgear Company Milwaukee, WI United States
|
Congratulations to the following CSIA Certified members:
AEA srl (Locciono) Italy
*McEnery Automation St. Louis, MO United States
*recertified
|
Contact Us
Leadership directory
________________
Get Connected
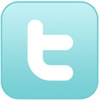
________________
Join CSIA
________________
Refer a new member! Tell your colleagues about CSIA. Find member benefits and an application at www.controlsys.org.
________________
Did you receive this issue from a colleague? Get your own copy! Register to receive the CSIA Newsletter on a regular basis here.
|
The CSIA e-newsletter is now available in Spanish. To be added to the mailing list, please contact Marcela Vallejo.
|
Quote of the Month
| |
"Making people smarter and more competent is the job of every leader. If your employees aren't growing and learning in their jobs, they're likely to leave and find better ones ... and that's especially true of the ones you would least like to lose."
- The Leadership Challenge, 5th Edition
|
|
The go-to resource for control system integration.
|
Best Practices Manual now available in Spanish
by Greta Mattison, CSIA Global Coordinator
We're excited to announce that the CSIA Best Practices Manual in Spanish is now available to our members! We are grateful to our CSIA LATAM Coordinator Marcela Vallejo, who helped make this possible. We also want to thank Eduardo Acosta and Omnicon for their assistance and commitment to this project.
During the past year, CSIA focused efforts on increasing and maintaining relevance of our organization for system integrators in Latin America. The translation of the Best Practices Manual demonstrates our commitment to this effort. While many system integration companies have staff who communicate in English, some employees do not. We want to share CSIA's best practices with all employees so that CSIA members are able to fully embrace these practices and improve their businesses company wide.
CSIA members may access the manual in the Best Practices and Certification - Members Only resource library in the CSIA Connected Community.
Don't forget - we also have the Best Practices Manual in Portuguese, thanks to Candice Ducharme and all those at MatrikonOPC who helped make this possible.
|
The Exchange continues to grow!
by Eric Huemmer, Exchange Community Manager
It is exciting to see how things are ramping up with the CSIA Exchange. We have been reaching out to members and nonmembers with targeted eblasts, and an astounding 65-plus individuals and companies registered within the first 24 hours of receiving one message! New companies and individuals are logging on daily, and we continue to see members updating their free bronze profiles and upgrading to silver and gold profiles.
The Exchange has also seen some great updates and additions to the site, including the introduction of a Premium Partner Package. Schneider Electric - Software and Opto 22 led the charge and took advantage of this great offer to combine a gold profile with advertising and networking to their SI program participants. Act fast, partner members, as this offer is available only until Aug. 15!
Questions about the Exchange? Contact Eric Huemmer or call 608-310-5575.
|
CSIA brand-awareness
A look at automation-related associations
by Bob Lowe, CSIA Executive Director and Don Ulrich, President of Stone Technologies and CSIA Board Member
Over the last couple months we interviewed the leaders of Manufacturing Enterprise Solutions Association (MESA) International, International Society of Automation (ISA), PI North America (Profibus/Profinet), Association for Advancing Automation (A3) and the Object Linking and Embedding for Process Control (OPC) Foundation. All of these associations focus on technology in the industrial automation space. We are seeking to learn how these associations manage their brand and the influence they have in the market.
Here are some of the highlights from our study, taken from a report we prepared for the Board of Directors.
- All have training and certifications particular to their purpose as an association.
- Brand awareness and brand misconceptions are challenges for all of them except ISA. ISA has been around long enough that everyone knows them.
- You can't market "on the cheap." All have a marketing staff. The more they spend on marketing the more successful they are.
- All use some combination of event attendance, licensing of for-profit companies to increase awareness, newsletters, short YouTube videos, websites, Twitter, whitepapers, media banner ads, webinars and road shows.
- A key to success is consistency of word and appearance, plus repetition.
Nine recommendations were made in the report to the board. Some require funds so those will be prioritized and considered for the 2015 budget. Those not requiring funds will also be prioritized and implemented by staff and committees as appropriate.
Our efforts on brand awareness and market influence are in response to the requests of our members to educate end users on the system integration industry, CSIA and CSIA Certification.
A byproduct of the meetings was building a relationship with the five organizations. We all serve the world of industrial automation but in different ways, so collaboration is underway. Some examples:
- Lynda Patterson attended MESA International's annual event to meet their staff and learn more.
- We will be sharing the OPC Foundation booth at the SPS IPC Drives event in Germany.
- Joint training efforts with ISA are being considered.
|
European integrator becomes CSIA Certified
We are pleased to announce that AEA Srl (Loccioni), located in Italy, has become our latest integrator in Europe to become a Certified integrator member. Congratulations to their staff that supported this achievement. CSIA thanks Armando Valim and National Instruments (NI), a partner member with which Loccioni does significant work, for their continued promotion of CSIA Certification to companies in their system integrator program. NI recognizes the value Certification brings to the integrator, to NI and most importantly to the end-user clients. Last month we congratulated GIL Automation in Nigeria, Africa. CSIA continues to increase its global presence and influence thanks to our staff, board and committee volunteers and members, both integrator and partner! |
Certification 101:
The Certification Management System
The new Certification Management System (CMS) has been in use for nearly a year and is working well, but we've learned that there is confusion. Yes, it has more steps than the previous system, but for good reasons. See the August 2013 newsletter for an explanation. Here are some basics of the process.
CSIA member companies that are interested in becoming Certified contact the CSIA office to begin the official process. A member profile form is sent to the company. The completed form enables staff to determine member eligibility for Certification and whether the company requesting it is a branch or head office. Other information helps the auditor prepare.
CSIA will assist in choosing an auditor, unless the member expresses a preference. If eligible, the integrator completes an application and pays the CSIA registration fee. CSIA enters into an agreement with the auditor. The auditor and integrator prepare and proceed with the audit. The integrator pays the auditor. CSIA receives no funds from the auditor and has no influence on the outcome of the audit.
Upon audit completion, the audit report is sent to the office for validation and compilation of data. CSIA staff uses the data to look for common strengths and weaknesses so that the Best Practices Committee can be informed and work to improve the Best Practices Manual. To maintain confidentiality, entries into the compilation spreadsheet are anonymous. CSIA staff receives the audit report (scores) of all audits, pass or fail, but no other information. If an audit is failed, the integrator and auditor continue working together on improvements necessary to pass the audit; there is no CSIA involvement.
Members are encouraged to download the CSIA Certification Manual for Members document from the Best Practices and Certification-Members Only library for a detailed explanation of the CMS.
|
WANTED! CSIA Certification Testimonials
"Improves internal processes." "Continuous improvement of project management." "Helps us stay focused on quality." These are some excerpts from member testimonials about the value of becoming and maintaining CSIA Certification.
Whether your company is newly Certified or have recertified multiple times, please send a few sentences that explain what drives you to take on this challenging task. Whether it's internal improvements, maintenance of your systems or external marketing, all reasons are significant. Please do it immediately, before you continue reading! Send a few sentences to Ann Nelson. We have Certified members on six continents now, so it would be wonderful to have testimonials from all six!
|

See all the archives on the webinar page.
COMING UP:
Wednesday, Aug. 20, 2014, 11 a.m., EDT (New York)
Leveraging Front-End Loading for Project Management Success Daniel Roessler, owner/consultant, DANR Consulting Front-end loading (FEL) studies result in more detailed scopes, improve estimates, increase schedule accuracy and help identify project risks. The benefits of shifting engineering activities forward are well documented, but FEL can also improve project management results. This presentation will examine how FELs present an opportunity for project managers to leverage FEL deliverables as the foundation for their project definition, progress monitoring and reporting, and change order management activities.
Daniel Roessler is the author of Control System Migrations: A Practical Project Management Handbook (Momentum Press, 2013). His career, spanning over 20 years, began as a process control engineer and project manager for a major chemical company. His background also includes roles as a project and proposal manager for a system integrator and business development and marketing manager positions with major automation vendors. Roessler is currently the owner of DANR Consulting, which provides content marketing, business optimization and project management services to engineering, software and manufacturing companies.

|
Integrator Marketing Committee - NEW!
A new committee has been formed to develop new ways to bring value to existing integrator members, make sure we are fully engaging current integrator members, and market CSIA to prospective members. The goal of the new Integrator Marketing Committee is ensure CSIA delivers value to system integrators everywhere.
Committee members are volunteers from large, medium and small integrator member companies so that the perspective of all company sizes will influence committee activities. The first task of the Integrator Marketing Committee is to finalize a survey on training to be sent to our integrator members. There is a list of other activities that the committee will prioritize and then move forward accordingly. All CSIA integrators are encouraged to support committee efforts. Stay tuned - more to come soon!
|
Should CSIA offer skills training? Let us know
In August, Integrator members will be asked to complete a survey on hard-skills training. Training is a product that CSIA wants to deliver but it's critical that we deliver what our members want and in the way they want it. There are many training programs available and we don't want to reinvent a program that's already available but rather fill important gaps. The survey requires about five minutes to complete and the link will be sent to only our member's primary contact. They can delegate it to others in their company if they choose. CSIA greatly values your feedback. It will enable us to provide meaningful training programs.
|
ARC Automation Index for the 1st Quarter of 2014
Manufacturing in North America contracted in the first quarter of 2014, primarily due to the unusually harsh winter and unusually small inventories. Elsewhere, Asia is rebounding and Europe is struggling with the Ukrainian crisis, according to the 2014 1st quarter Automation Index executive summary.
CSIA members receive the report as part of CSIA's annual agreement with ARC Advisory Group. This tool provides ongoing coverage of manufacturing and enterprise issues, trends and technology and how they affect your business. ARC collects data from major automation vendors and analyzes the results. Use this insightful analysis to enhance your value premise, improve your go-to-market strategy and attain competitive advantage.
|
Opportunity is knocking at the Windows!
by Glenn Graney, GE Intelligent Platforms, Platinum Sponsor of the 2014 CSIA Executive Conference
The integrator community is well aware that Microsoft stopped supporting Windows XP on April 8, 2014 - including security patches. Microsoft has only committed to providing malware updates through July of 2015. Windows XP is the underlying operating system for countless numbers of installed HMI/SCADA solutions across the industrial landscape.
Opportunity for system integrators is knocking on those Windows. There are attractive and important service projects associated with moving our clients forward. Despite the clear forcing-function there are customers without clear migration plans. The SI is the trusted advisor who can help build the case for the investment. The risks are fairly obvious:
- Unsupported OS and associated security increases the risks of virus or data protection issues.
- Unsupported OS on aging hardware increases can result in major downtime
- Unsupported OS greatly limits the ability to embrace application fixes and potentially beneficial upgrades to software.
A challenge for many installations is justifying the ROI for an infrastructure upgrade without an obvious positive impact on the water being treated or the product being manufactured. However, a well-informed discussion between SI and end user can result in a plan that diminishes risk, puts the appropriate rigor around security and identifies real benefits for the transition.
Opportunity for significant service projects with significant end-user benefits are knocking loud and clear - just open the Windows and let them in!
|
Phoenix Contact USA expansion drives the push for energy efficiency
by Steve Newcomer, Phoenix Contact, Platinum Sponsor of the 2014 CSIA Executive Conference
In the spring of 2014, Phoenix Contact completed a major expansion to its U.S. headquarters near Harrisburg, Pa.
To accommodate the growing number of employees and specifically meet the needs of its development and manufacturing business, Phoenix Contact doubled its U.S. manufacturing footprint to 90,000 square feet. It also added a three-floor tower with 50,000 square feet of space for engineering offices and labs.
This construction gave Phoenix Contact the opportunity to improve its energy footprint. In March 2014, a combined cooling, heating and power (CCHP) system went online, allowing Phoenix Contact to generate enough electricity to operate independent from the power grid about 65% of the time.
The CCHP consists of five natural gas-powered microturbines that can generate up to 1 megawatt of electricity. The system also heats and/or cools the 360,000-square-foot facility, independent of external sources. As the microturbines generate energy, they vent the exhaust heat byproduct through either the building's absorption chiller or its heat exchanger to regulate the temperatures of the building's chilled and hot water supplies. That demand will determine how much electricity the system will generate, while reducing the amount of waste Phoenix Contact produces.
The system will save Phoenix Contact more than $300,000 per year. The additional electricity generation source provides redundancy, so that if either Pennsylvania Power & Light (Phoenix Contact's electricity provider) or the CCHP itself goes out of service, the facility can continue to operate. To ensure reliable and efficient operation, the controls for the CCHP system rely heavily on Phoenix Contact products.
While the CCHP was the largest project so far in improving the facility's energy efficiency, it is just one step in an ongoing sustainability strategy. The company has already implemented ISO 9001, 14001 and 18001 certifications and is working toward 50001 (energy management). Other goals include a zero-landfill target by 2020 and possibly adding solar panels to the facility's roof in 2015 - another step toward independence from the grid.
|
Reshoring: good news for system integrators
by Harry Moser, Reshoring Initiative
Automation is key to reshoring. Reshoring is a great opportunity for selling automation, which is involved in about 40% of reshoring cases. The Reshoring Initiative is a nonprofit organization dedicated to helping companies understand the true cost of offshoring by using total cost of ownership (TCO) analysis. Our mission is to bring well-paying manufacturing jobs back to the United States and shift collective thinking from offshoring is cheaper to local sourcing reduces the total cost of ownership.
The same logic and calculations apply to all countries. Reshoring efforts are underway in France, the United Kingdom, Canada, Korea and the Netherlands. Nearshoring is sometimes the right solution, e.g., with work coming back from China to Mexico.
TCO is defined as the sum of all relevant costs, risks and strategic impacts associated with making or sourcing a product domestically or offshore. TCO includes current period costs and best estimates of relevant future costs, risks and strategic impacts, e.g., warranty, intellectual property loss and impact on product innovation.
Companies are often faced with a decision of whether to take the easy way out and offshore production to low wage countries or do the heavy lifting associated with automation, lean and skilled workforce training. If the company bases its decision on the ex-works price, which might be 30% lower offshore, it will probably conclude that it is impossible to overcome such a large gap. However, if the company uses TCO and sees that the real cost difference is only 5 or 10% and shrinking, the ROI on automation just went up substantially. We can help train your sales team to use TCO to justify automation and bring work back.
Based on user data, about 25% of offshored work is reshorable with current levels of productivity. More productivity increases that percentage. A great way to demonstrate the benefit of automation is to publicize how it helps with reshoring. You can report your clients' reshoring successes. The TCO Estimator and other Reshoring Initiative tools are available for free online. Let's work together to automate manufacturing and bring work back to your home country!
or +01-847-726-2975 (Illinois, US).
|
CSIA members make headlines
 Members that have been featured in industry media recently include: Autoware Managing Relationships Among Operations, IT and Engineering Automation World Avid Solutions 3 Tips for Safe and Effective Virtualization Concept Systems Reduce Risk and Costs by Improving Project Selection Automation World Loman Control Systems How to Develop a Project Plan Automation World |
|
|
|
|