Greetings!
Welcome to the first of a continuing series of articles on Collins' UV Curable Ink. This three newsletter series will discuss current and future trends of digital UV technology, from our perspective. Collins has witnessed many recent advances in UV that are quickly changing the industrial printing industry. As our business continues to grow and customers adopt this relatively new technology, we're learning a lot. We hope you find this series as exciting as we do!
|
What is UV Curable Ink?
UV curable inkjet is the fastest growing ink segment in the digital market, far surpassing aqueous and solvent based inks. UV curable inks typically contain reactive monomers, photo initiators, oligomers, pigments and additives that, when introduced to an ultraviolet (UV) lamp, creates a rigid film.
The current market for UV curable inkjet can be divided into two categories: wide format graphics and industrial (single pass), with textiles soon creating a category of its own. The reason for UV's growth can be attributed to its excellent print quality, color intensity, adherence to non-porous substrates, instant "dry" time, no VOC's, and more.
The graphic arts market encompasses all types of "pay for print" jobs, such as signage.
The industrial print market is extremely varied and includes any type of printing to impart functionality or decoration. For example: Printed circuit boards, medical devices, tickets, novelty items, labels, packaging, automotive components, various industrial pieces. Collins has created several platforms of UV curable inkjet inks to address both the graphic arts and industrial printing markets.
|
UV for Pharma, Bell-Mark's Story
|
In package printing, consistent, high resolution print quality is vital. Bar codes, lot numbers, expiration dates, and other variable data must be easily readable, identifiable, and scan-able. When printed packages contain pharmaceutical items, the coding requirements are amplified because of the associated health and safety risks. The FDA actually mandates the printed data. An accurate, reliable code can be the difference between success and failure, and this is something with which Bell-Mark has experience.
Since 1959, Bell-Mark has been successfully designing, manufacturing, and servicing high-performance coding, marking, and printing equipment for the industrial marketplace, reaching over 15,000 companies throughout the world. A significant portion of Bell-Mark's business is in the pharmaceutical and medical device industries. Like many package printing customers, Bell-Mark's customers are looking for a printing technology that can meet the rigorous demands of packaging environments, print high resolution images quickly, and employ a small equipment foot-print. "High definition inkjet technology is a perfect fit, due to its high quality of print, as well as its versatility," says Bob Batesko, Director of Sales for Bell-Mark. When evaluating the different digital ink types, Bob says that they decided from the beginning to integrate piezoelectric printheads using UV curable inkjet inks. "One of the major problems with inkjet technology is clogged jets. By utilizing UV, we all but eliminate the ink drying in a nozzle, and this results in less cleaning, flushing, and downtime," says Bob.
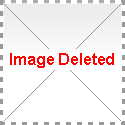 |
|
Bell-Mark approached Collins regarding a Tyvek printing installation utilizing the Kyocera KJ4A printhead, where dry time was an issue. Muslim Contractor, Collins' Lead UV Chemist, recalls that "the existing ink wasn't formulated specifically for a UV- LED curing lamp, so in order to run, the production line needed to slow down significantly." Upon receiving the customer's stock samples, Muslim formulated a custom black UV-LED curable ink that both cured quickly and created a permanent, dark image on Tyvek. "Having the ability to jet and cure UV/LED inks through Kyocera printheads, gives us some certainty that the ink would perform as required on Bell-Mark's substrate," he adds. After receiving the customized black, Bob reports, "We have had excellent results. I would certainly recommend Collins' UV-LED curable black ink. The company has been excellent to work with and the product has performed as advertised."
Collins has built its business on formulating and manufacturing industrial inkjet inks that are tailored for specific applications. The new UV and UV-LED industrial printing spaces are no different. Unfortunately, there isn't a "one size fits all" fluid that will do everything for everyone on every substrate; for those new adopters of digital printing who come from traditional printing, this is a difficult learning curve. Each situation is different, and, in most cases, the ink is the afterthought and therefore the variable. Similar to Bell-Mark's case, the ideal solution is collaborative communication between integrators, printhead and UV lamp manufacturers, ink and substrate suppliers, customers, etc. This allows everyone to do what they do best to quickly create a successful situation. Often times, this is not the case, and the successful ending takes a while longer to reach.
Today, Collins' customers are pioneering UV Curable technology into new markets and applications, challenging its capabilities and limitations. This is an exciting time for the digital printing industry and UV is leading the charge. Collins will continue to welcome customer's challenges and formulate exceptional UV inks that push the envelope into the future of print.
|
Flexible Substrates
The Collins C-Flex line of UV Curable inkjet inks was designed to perform in demanding industrial applications where a high degree of elongation and forming is required. UV curable inks are inherently brittle because cross-linking and shrinkage occur with polymerization. However, Collins' patented C-Flex inks allow elongations of >300% while maintaining adhesion and image quality.
These inks perform well in a variety of piezoelectric, drop on demand, printheads, resulting in high quality prints that may be flexed and formed for industrial applications. Curing for these inks is achieved using a mercury lamp at 300 Watts/inch or higher, at an energy density of 200 mJ/cm2 or higher.
Industrial Applications Include:
- Fleet graphics for vehicle wraps
- Automotive appliques
- Post-formed parts (see image)
- Shrink wraps
- Blister packaging
- Flexible materials for signage
- Embossed parts
|
If you have any questions regarding this newsletter, or anything else, please contact us today. You may also view Collins' current product portfolio by clicking here
Sincerely,
Kristin Adams (513) 948 9000
|
|