|
|
Seasons Greetings from the BEASY team
|
As we approach the end of 2015 in this issue of the newsletter we recap on some of the BEASY news stories we think you will find of interest.
|
In early 2015 the NACE Corrosion Conference in Dallas provided the opportunity to present recent developments and applications in the technical sessions and exchange groups.
It was great to meet many friends at the conference and discuss how modelling can be used to improve and optimize CP systems, as well as providing further confidence in their performance as part of "due diligence" activities.
In addition to the activities by BEASY staff there were papers presented at NACE incorporating BEASY modelling, including:
|
Application Of Linear Anodes To Protect Isolated And Unisolated Piping In A Petrochemical Plant
Mobeen Hassan, Sharjah, United Arab Emirates & Stephen Wroe Corrosion Technology Services LLC Sharjah, United Arab Emirates
The paper describes an application of cathodic protection using linear anodes in a congested petrochemical plant in the Middle East. The initial design of the cathodic protection is discussed along with the problems found due to faulty isolating flanges and loss of current to other structures. Computer modelling of a typical electrically continuous cathode including steel in concrete and earth rods is included to demonstrate the need to consider all components of complex structures. Lessons learnt from this case study are applicable for the application of cathodic protection in plant using distributed anodes.
The results shown below illustrate the effect of adding continuous reinforced concrete paving into the circuit. The dramatic effect is that the pipe potentials are hardly shifted from the natural potential even with the anode operating at 100mA/m.
BEASY will be exhibiting at the NACE Corrosion Conference in Vancouver in March 2016 as well as presenting a number of papers in the technical conference. If you wish to make arrangements to meet with BEASY at the conference please contact us.
|
|
NACE Materials Performance magazine
There were also two articles published in the last year in the NACE Materials Performance magazine which featured modelling performed using the BEASY software:
|
Designing an ICCP System for the Hull of an Arctic Ice-Breaking Vessel
Researchers used modelling tools to design effective cathodic protection systems that address challenging seawater conditions and coating damage from ice abrasion.
According to researchers Min-Jeong Lee, senior engineer, and Chae-Seon Lim, principal research engineer, both in the Material & Coating Research Department at Samsung Heavy Industries, Co., Ltd, South Korea, the performance of a CP system for a ship's external hull is dependent on several factors, including the geometry of the ship's hull, the resistivity of the surrounding seawater, the chemicals in the seawater, and the degree of coating damage. The ICCP design for many commercial vessels is often based on current density (CD) calculations and the designers' experience rather than an analytical method. For an icebreaker travelling in Arctic conditions, the researchers note, this traditional approach to CP design may not result in an adequate amount of corrosion protection for the hull in this environment.
To determine the optimum ICCP design for the external hull of an icebreaker, the researchers explored a modelling approach using computational analysis based on the boundary element method (BEM). Lee comments that modelling tools are often used to design ICCP for stationary offshore structures such as oil and gas production platforms; floating production, storage, and offloading (FPSO) units; and semi-submersibles.
Using computational analysis and modelling was successful in determining that an ICCP system design is effective for a vessel exposed to Arctic seawater conditions. Going forward, Lee expects more use of CP modelling when designing ICCP systems for ship hulls, particularly those headed for the Arctic.
For further information, please contact BEASY at info@beasy.com or to view the article, published in the March 2015 issue of Materials Performance, please click here
|
|
|
The article looked at the effect of grounding on the cathodic protection (CP) potential distribution at an oil station, which had been studied using BEASY's corrosion and cathodic protection simulation software.
Influences from four factors were analysed: grounding system material, relative position between the grounding conductor and the pipeline, and length and buried depth of the grounding conductors. CP designs with and without grounding were compared.
For further information, please contact BEASY at info@beasy.com or to view the article, published in the March 2015 issue of Materials Performance, please click here
|
Aircraft Airworthiness & Sustainment Conference
BEASY staff attended the 2015 AA&S Conference in Baltimore in and met with many customers to discuss their applications and update them about projects underway at BEASY.
An area of considerable interest at the AA&S conference was the use of computer simulation to assess the risks associated with corrosion. During the product development process, various design configurations are often exposed to actual environmental conditions for an extended period of time to evaluate corrosion damage in the structural assembly. However, these testing methods require anywhere from several months to several years of exposure time in order to complete. Computer modelling has the potential to significantly shorten, and reduce, the cost of testing by providing a corrosion simulation option that can be used to supplement these long term experimental tests.
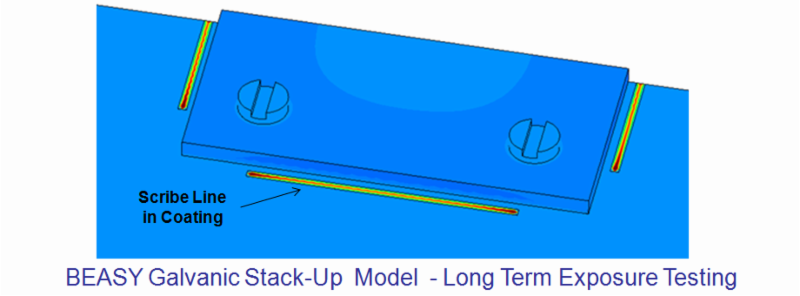
In the model shown a computer simulation is used to predict the risk and extent of corrosion damage on a test structure.
|
International Committee on Aeronautical Fatigue and Structural Integrity (ICAF) Conference in Helsinki, Finland
Dr Sharon Mellings from BEASY attended the ICAF conference in Helsinki and presented a paper describing some recent work on the simulation of corrosion and fracture damage.
Airframe structures regularly operate in environments that allow high levels of corrosion damage, and this damage leads to stress concentrations within the structure and potential development of cracks. Even when only a thin film of electrolyte is present on the structure, this can still lead to an electrical field that causes surface damage.
Computation of this electrical field can be used to identify areas in the airframe structure that are most susceptible to corrosion damage and which, after possible fatigue crack initiation, may lead to structural failure. Corrosion simulation can be used to take account of the properties of the electrolyte as well as the structural materials, to determine the rate of material loss from the structure.
In this conceptual development, material is removed from the modelled surface (corresponding to corrosion occurring over a given exposure time) the stress concentrations can be evaluated and, if required, cracks can be introduced into the identified problem areas, to identify vulnerability to fatigue failure.
The geometry change caused by corrosion mass loss can be used to perform stress analysis of the structure, to determine the stress concentration in the component at the corresponding time in the life of the aircraft. If it is then assumed that cracks initiate at the peak stress locations, the subsequent crack growth can be simulated. This crack growth takes into account the corrosion damage and will inherently include local stress concentration due to the damaged surface. In the crack growth simulation, the full crack path and direction can be determined together with the fatigue life.
For a copy of the paper, or for more information about corrosion and fracture simulation, please contact us
|
Christmas & New Year holidays
The BEASY offices in the UK and USA will be closed for the Christmas and New Year holidays, but if you would like to learn about any of the items above, or if you have a project which you would like to discuss, please contact us
|
Canada Anti-Spam Legislation
On July 1, 2014 new laws were implemented that regulate how we can communicate electronically with our contacts in Canada, and we would ask that you reconfirm your newsletter subscription by clicking on the button below.
|
By confirming your subscription you're granting us permission to email you. You can revoke permission to mail to your email address at any time using the Safe Unsubscribe link found at the bottom of every newsletter.
|
|
|
|
|