~~~~~~~~~~~~~~~~~~~~~~~~~~~~~~~~~~~~~~~~~~~~~~~~
Pam East Newsletter - March 2010
Metal Clay & Enamel projects, tips & tricks, and general announcements
~~~~~~~~~~~~~~~~~~~~~~~~~~~~~~~~~~~~~~~~~~~~~~~~ You are receiving this email because you subscribed to recieve my newsletter. If you do not wish to continue receiving these newsletters, you may use the "unsubscribe" link at the bottom of this message. ~~~~~~~~~~~~~~~~~~~~~~~~~~~~~~~~~~~~~~~~~~~~~~~~
|
~~~~~~~~~~~~~~~~~~~~~~~~~~~~~~~~~~~~~~~~~~~~~~~~ Greetings!
Do you need a kiln to try out enameling? This question has been coming up a lot recently, so I decided to dust off an article I wrote many years ago, update it a bit, and share it here with you. This month's project is making silver and enamel earrings using only a gas stove top!
Also, I have just opened up a one day class for Art Clay Copper on March 26th. I know this is short notice, but I hope you'll be able to join us! More information below.
Pam East
~~~~~~~~~~~~~~~~~~~~~~~~~~~~~~~~~~~~~~~~~~~~~~~~
|
|
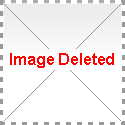 NO KILN? NO TORCH? NO PROBLEM! Stove Top Enameling with Art Clay Silver 650
Have you been holding off on trying Art Clay Silver and/or enameling because you didn't have a kiln or a torch? Then I've got great news for you. All you really need is a gas stove. Even if you don't have a gas stove, you can use a propane camp stove. Single burner camp stoves are available at places like Wal-mart for around $20.
Here's what you're going to need: 20 grams Art Clay Silver 650 Low Fire Clay Roller Graduated slats set (or cards) Texture sheet or stamp Teflex or plastic report cover Badger balm or Olive oil Stencil brush Straw Wire brush Burnisher Long Tweezers Glass brush Ammonia 80 mesh enamels Firing Screen Small sifter Klyr-fire with sprayer 200 mesh sifting screen Dust Mask Gas stove or Propane camp stove
Not sure where to find these items? It's all available from the suppliers listed on the Resources page of my website.
Creating an Art Clay Silver Piece to be enameled:
-
Prepare your workspace by applying Badger Balm or Olive oil to your hands, roller, Non-stick reusable work surface (teflex or a piece of a plastic report cover). Use just a little. Your tools should not appear greasy or oily.
-
Your texture sheet stamp will need to be lightly coated with olive oil or badger balm as well. I use an inexpensive toothbrush to apply it. Again, only a very tiny bit. Oil should not pool in your texture.
-
Place a pair of slats a few inches apart on your texture. Slats are plastic strips that allow you to roll out your Art Clay to an even thickness. Color coded slats of various thicknesses are easiest to use, but playing cards may be used as well. If using color coded slats, I recommend the blue set. This is equivalent to 4 playing cards.
-
Place the Art Clay Silver on the texture sheet, between the slats, and use the roller to roll it out. By keeping the ends of the roller on the slats, you will maintain an even thickness.
-
Remove the clay and turn it textured side up on your non-stick reusable work surface. Cut out a shape for your piece. You can use small cookie cutters, a craft knife, or any other cutting tool. U
se a small straw to cut a hole in the piece so you can hang it from a jump ring later.
-
Set the piece aside and allow it to dry completely. If you are air drying it, let it dry at least 24 hours. You can also use a food dehydrator, a hotplate, or a hair dryer to speed the process along. It's very important that it be completely dry before you fire it.
-
Once the piece is dry, use sandpaper or sanding pads to smooth any rough edges.
-
Find the "hot spots" on your stovetop before firing. Place your firing screen on your gas burner (stove top or camp stove), and turn the burner on high. In a few moments, parts of the screen will begin to glow red. These are your "hot spots" and you want to make note of where they are. Turn off the burner.
-
Now you're ready to fire the piece! Use a pair of tweezers to place the piece to be fired on one of the hot spots on the screen. (the screen may still be hot from your test, so don't use your hands)
-
Turn the burner back on high. Wait for the piece to turn a light peachy orange color, and then start a timer for at least 5 minutes. When the timer is done, turn the stove off, but leave the piece in place on the screen for 20 minutes.
-
Once the piece is cooled it will need to be burnished. Begin by brushing it vigorously with a brass wire brush. Final burnishing can be done with an agate burnisher, or in a rotary tumbler with stainless steel shot.
Ok, your piece is now finished and ready for enamel!
When choosing which colors of enamel to use, avoid reds, yellows and oranges. These colors react with silver and turn an ugly yellowish or brownish color when fired. You'll have better luck with blues, browns and greens. Some purples, such as Rose Purple and Concord work well too. I suggest using transparent enamels rather than opaque. You want the pretty silver to shine through!
SAFETY NOTE: Please wear a dust mask with a good seal around your nose and mouth whenever you are screening or sifting enamels! These processes put glass dust in the air. A good dust mask can be purchased at Home Depot, Lowe's or any other hardware store. Be sure and get a true particle mask, and not just a "comfort mask". Look for N95 or N100
-
Begin by preparing your enamels. Transparent enamels can sometimes appear cloudy unless they are screened first. This is caused by very fine particles in the enamel. Use a 200 mesh screen to remove the fine particles. Place the screen over a clean sheet of paper. Place a small amount of enamel to be cleaned in the sifter. (don't forget the dust mask!) Place a clean quarter in with the enamel. The weight of the quarter greatly speeds the sifting process. Gently shake the box back and forth until all the fine particles have been removed.
IMPORTANT: You will be using the enamel that remains in the screen, not the fine particles that sift out onto the paper. Just fold up the paper with the fine particles and throw it out.
-
The sifted enamel can be placed in a plastic spoon for the time being. I find it's helpful to write the name of the color on the handle of the spoon with a marker. Repeat this process for all the colors you want to use.
-
Clean your silver piece with ammonia and a glass brush. This removes any dirt, oils or soap left from the burnishing. Rinse with clean water and dry.
-
Lightly spray the piece with Klyr-fire enamel adhesive. Klyr-fire should be diluted 1:1 with water and put in a sprayer. Do NOT spray directly onto the piece. Rather, spray above it and let the mist settle down on to it.
Place the piece on a clean sheet of paper.
-
Pour a little enamel into a small 80 Mesh sifter. Hold the sifter over the piece and run your fingernail along the handle. The handle is twisted, so this will cause a vibration that will sift out the enamel. Gently sift on a layer of enamel. Using the same steps, additional colors may be sifted on to create shading or color variation.
-
Use a small paint brush to gently clear the enamel from the highpoints of your piece. Place the piece on the firing screen on your stovetop burner, positioning it over the hotspot.
-
urn the burner on to high. If you see the piece is not centered over the hotspot, you can use a pair of long tweezers to move the screen. Move the screen, NOT the piece being enameled. This will avoid any unhappy spills.
-
Watch the enamel as it fuses. It will first appear granular, then it will proceed to an "orange peel" stage, and finally it will smooth out to a glossy surface. When it reaches the glossy state, turn off the burner and let the piece cool.
- Shine up the exposed silver areas using a polish cloth or tumbling it again. Tumbling should not hurt the enamel.
That's it! You're done! You can repeat the enameling steps if you like to fill in areas that were missed, or to provide deeper color or shading. I do not recommend more than two coats, however. If the enamel becomes too thick it could crack.
I hope you'll give stovetop enameling a try. It's quick, easy and fun. |
~~~~~~~~~~~~~~~~~~~~~~~~~~~~~~~~~~~~~~~~~~~~~~~~
Intro to Art Clay Copper
March 26, 2010 - 10am to 5pm
Johns Creek, GA
Ready to learn all about copper clay? Come join me for a one day intro class in Art Clay Copper! We'll do a variety of beginning projects. Topics will include working with the wet clay, drying, firing and finishing.
Space is limited so sign up early!
| |