GRIDLINE, Issue #12, January 2015
|
|
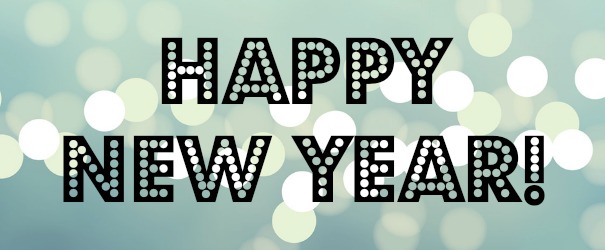
Recently Completed Techline Series Covers Strong & Weak Direction Panel Splices
We recently completed a series of four technical bulletins (listed below) that explain common methods used to connect panels for grid reinforced concrete and Exodermic® bridge deck systems. These technical updates provide examples for weak and strong direction panel splices for both precast and cast-in-place bridge deck installations, which fits well with continuing initiatives promoting ABC technology.
You can find these documents, along with additional bulletins and reports covering various frequently asked technical questions on our website. However, if you do not find the information you are looking for on our website, please do not hesitate to contact us.
|
Georgia DOT Used Precast Grid Deck Panels to Accelerate Rehabilitation of I-20 Bridges
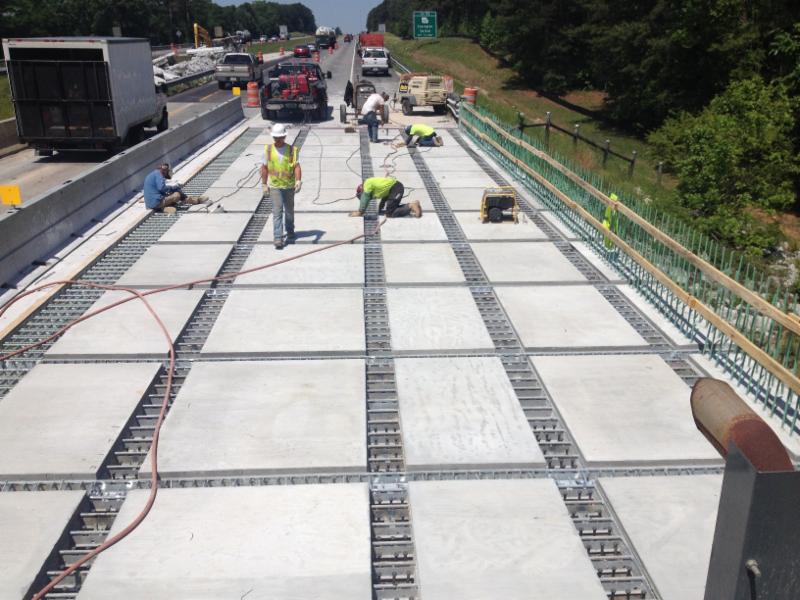 | Figure 1: Precast grid deck panels in place. |
The Georgia Department of Transportation maintains a network of roads and bridges that carry some of the highest traffic volumes in the country, and often employs accelerated bridge construction products when rehabilitating their structures. As was the case in the recent rehabilitation of two eastbound and two westbound structures spanning the Alcovy River and Alcovy Watershed on Interstate 20 located in Newton County just 35 miles east of Atlanta. This stretch of I-20 is a major route for over 40,000 commuters per day, as it connects Atlanta to Augusta, and other popular destinations to the east. A viable detour route was not available to permit full bridge closures, so with the interest of the traveling public in mind the DOT required staged construction with the bridges fully open to traffic during peak travel times. In late 2013, the Georgia DOT awarded Massana Construction, Inc. the rehabilitation contract that included deck replacement, painting and other miscellaneous repairs to the four bridges.
The Georgia DOT correctly realized the highest traffic volumes on this stretch of I-20 occur during weekends and holidays. In an effort to eliminate disruptions to weekend travelers, the DOT only permitted weekday lane closures from 12:00 noon on Sunday until 10:00am on Friday, with a $500/hour penalty charged to the contractor for late opening. To reduce weekday traffic congestion during construction, only one lane could be closed at any time on either the eastbound or westbound structures. Staged construction with short five day closures was possible using precast grid reinforced concrete bridge deck panels, with two unique details utilized to connect the panels. One detail used a simple shear key splice, and the other used overlapping shear studs in the negative moment regions over the piers to develop tension in the panels. Rapid setting concrete was used for the closure pour areas over the supports and between panels, allowing traffic to be put back on the bridge less than one day after the pour.
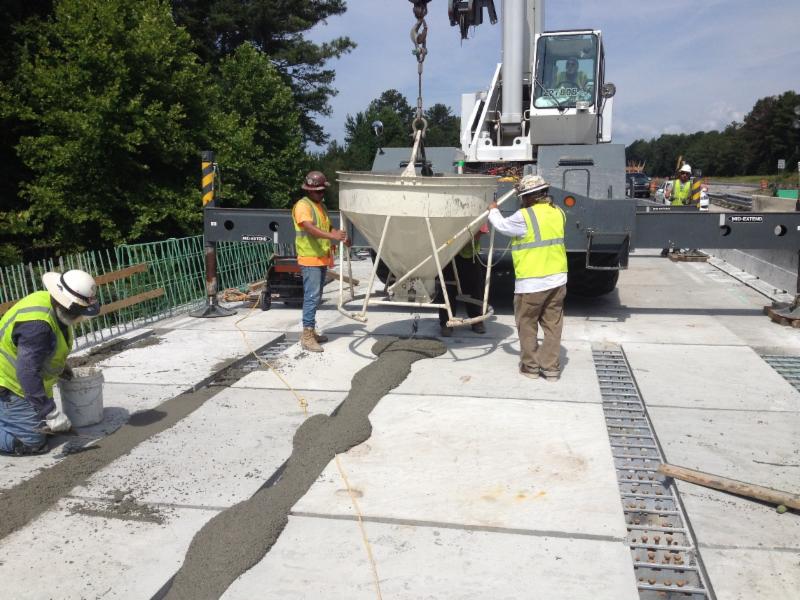 | Figure 2: Closure pours. |
The 208 galvanized grid deck panels were supplied by Bailey Bridges, Inc., a fabricating member of the Bridge Grid Flooring Manufacturers Association (BGFMA). The panels were precast less than 60 miles from the project site at Massana Construction's own precast yard in Fairburn, GA. The precasting operation was efficient and required very little formwork, keeping costs to a minimum. Massana was able to replace nearly 34,000 square feet of bridge deck from April 21st to August 11th, 2014. In that timeframe there were 17 weeks, however four weeks were lost to holidays and weather and another four weeks were required for MPT work, leaving only 9 closure periods for deck replacement. According to Steve Roeser, Project Manager for Massana, "There was only a short learning curve needed when working with the precast grid deck panels. After the first few weeks we were running at full speed, replacing roughly 5,000 square feet of deck (26 panels) in each closure."
|
Newburgh-Beacon Bridge Deck Replacement Utilizes Custom Engineered Grid Panels
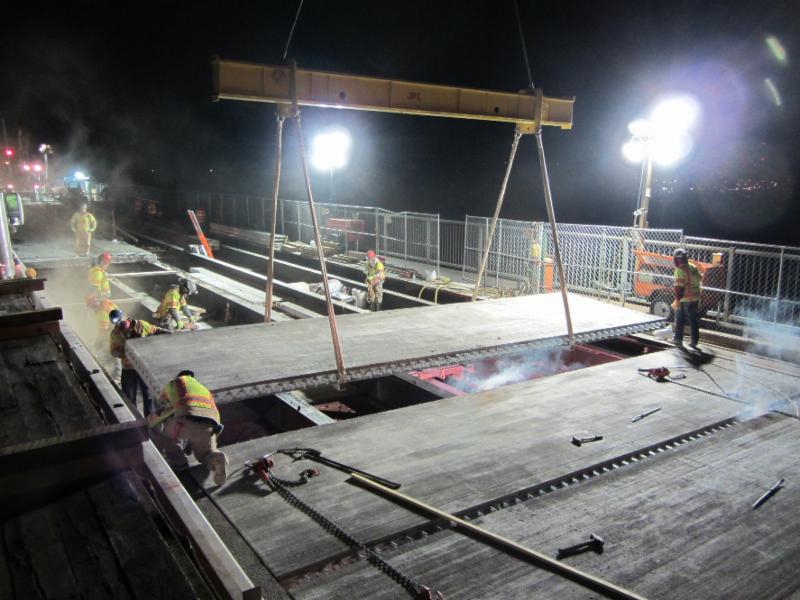 | Figure 3: Setting precast grid deck panels. |
The nearly 8,000-ft long Hamilton Fish Newburgh-Beacon Bridge is the busiest of 5 toll structures owned and operated by the New York State Bridge Authority (NYSBA). It's comprised of parallel articulated truss spans that carry more than 25 million crossings per year on NY Route 52 / I-84 over the Hudson River between Newburgh and Beacon, NY. The original two-lane bidirectional north span was opened in 1963, but in just one year traffic volumes exceeded the capacity. To accommodate the increased traffic, a parallel south span was opened in 1980 with three vehicular lanes and shoulders on each side, and a separated sidewalk for pedestrian use. Currently each of the twin spans carries three lanes of traffic in opposite directions. Over 30 years of heavy traffic on the south span deck took its toll, and in early 2013 Kiska Construction Corp. USA was awarded a $93.5 million, 430,000 square foot deck replacement contract.
The contract required a durable new deck system and a construction sequence that minimized daily traffic disruptions to commuters, which is where custom engineered grid reinforced concrete deck panels came into play. The plan, developed by Ammann & Whitney along with input from the NYSBA, involved nighttime panelized deck replacement utilizing precast grid panels with full depth concrete. Precast grid deck systems are common when accelerated construction is needed, and are typically attached to the structure like any other precast concrete deck via headed shear studs and a concrete haunch closure pour over the supports. What is unique about the 1,850 grid deck panels being used on the Newburgh-Beacon Bridge is the method used to attach them to the supports below, which does not require a concrete haunch closure pour.
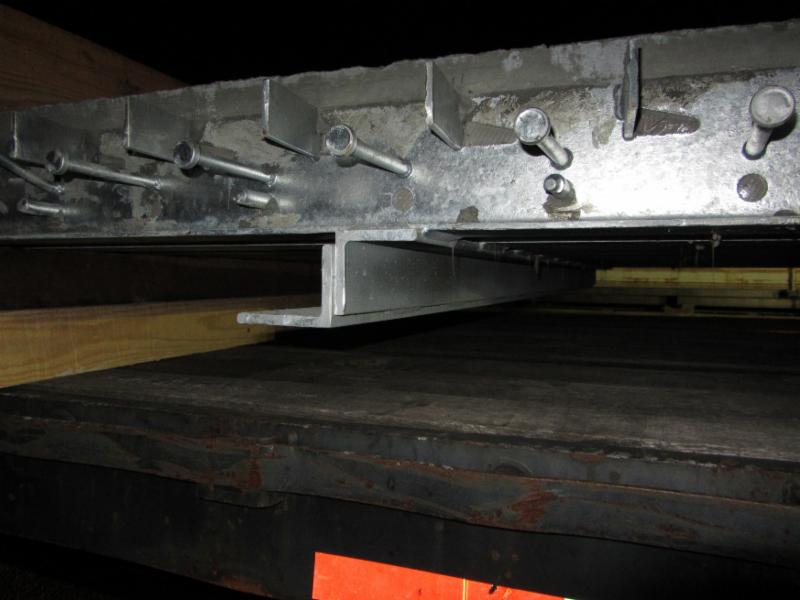 | Figure 4: Steel angles attached to grid deck panel. |
Details for the Newburgh-Beacon Bridge utilize steel angles shop welded to the bottom of the grid main bars (see figure 4), which are then field welded to the supports by the contractor. LB Foster, a fabricating member of the BGFMA is supplying the steel grid panels to Kiska, and also played a key role working with the owner, consultant and contractor prior to fabrication to develop the required deck connection details. Attention to small detail and accurate field measurements were critical during the early stages to ensure proper fit-up during construction, as an aggressive replacement schedule allows little room for error using precisely sized precast panels and the welded angle attachment.
The project is currently underway and scheduled to be complete in late 2015. So far the project is moving smoothly without any glitches, and the reduction in required closure pours as a result of the unique deck connection detail has helped accelerate construction with Kiska replacing nearly 3,000 square feet of deck during each nightly closure. Another benefit to the field welded attachment method is that it will allow the owner to replace deck panels on an individual basis if they are ever damaged.
|
|
|
|
|