|
|
2010 Luthierie Camps...F5 Mandolin Construction:
Feb. 21-26, 2010 April 25-30, 2010 Oct. 10-15, 2010
H5 Mandola Construction:
July 18-23, 2010
Please visit our website or email Kali for more information about these programs.
|
|

Dear Luthiers,
It's hard to believe that another year
has zipped by.
2009 was an exciting year for us; a new
shop, lots of new tooling, many new products, new luthierie friends, and our
first (and very successful) Siminoff Luthierie Camp. We have more in store for
you this year, and we look forward to working with you on your building
projects. I think most of you know that one of our two main goals is to provide
unequalled service and support (the other goal is to provide you with excellent
product). While we can't be at your workbench, we want to be as close as we
can.
And, while on the topic of working with
you, I want to personally thank you for your continued interest in our products
and services, and thank you for your trust and your business!
Our next Luthierie Camp is the week of
February 21-29. This is an intensive five-day program on building the F5, and it
covers a wide range of topics from musical acoustics to finishing, and
everything in between. During the week, our campers will build an F5 and leave
with a fully assembled instrument in "white wood" ready for fretting, binding,
and finishing. To learn more about this program, here's a quick link to our
Luthierie Camp page.
IMPORTANT: We have just received a
cancellation for our February Luthierie Camp. If you are interested in
attending, please go to our site and download an application form, or better
yet, give our Camp Director, Kali, a call at 805.365.7111 so she can mail you
an application packet today.
From all of us, here's wishing you an
incredible New Year!
Thanks for building with us...
Roger
|
|
What was Loar hearing?
The interest in tap tuning has grown
tremendously over the past five years and many builders cite my book, The Art of Tap Tuning, as the source for
tap tuning inspiration and information.
As most of you know, one of the
interesting features of the Gibson F5 mandolins that were signed by Lloyd Loar
in the early 1920s is that they were tap tuned - a key attribute that gives
these instruments their unusual rich and powerful tone.
In February of 2006, the California
Bluegrass Association (CBA) held a "LoarFest" in Bakersfield, California during
which 25 owners of Loar-signed F5s (including the one in our possession)
brought their mandolins for all to see and hear. As we listened to each of the
instruments being played in the same room, it was both interesting and unusual
to note that each instrument had a very similar tone. Aside from the fact that
most of the instruments had different types of strings, and were being played
by different people with different picking styles and different types of picks,
there was a common thread among all the instruments unlike what one might hear
from any grouping of 25 other mandolins. It was uncanny.
The similarity of tone in the F5s wasn't
coincidence - it was very much by design, and the key attribute was the fact
that these instruments were tap tuned.
As I think most of you know, tap tuning
is the art adjusting the stiffness of the wood and the size of the apertures to
literally tune the various parts of the instrument to specific notes. The
process is much as if you were making xylophone bars and had to remove wood
until you arrived at the desired frequency for each bar.
But what is most interesting is that the
concert pitch Loar was applying in the 1920s was not the same as the concert
pitch we use today. In Loar's time, concert pitch was C=256 (when C=256, A=431). Today, concert pitch is A=440 (adopted as the standard in 1971).
So, here we have the case of Loar requesting that F5s were tuned to notes in
the 1920s that we don't use in 2010. In fact, C=256 is actually a quarter-tone off of A=440. This poses a very interesting question. Is what Loar was hearing
in 1920 different from what we hear today?"
The answer is most probably, "yes!"
Loar did experience A=440 since the change to that concert pitch as the standard was
being considered by leading worldwide music organizations before Loar's death
in 1943. (In fact, I have owned several of Loar's personal keyboard instruments
some of which he had tuned to C=256
and others tuned to A=440.)
As an interesting and surprising
experiment, tuning the strings of a Loar-signed F5 to concert pitch C=256 (A=431) yields an instrument that doesn't really sound very good.
Same strings, same pick, same player, just tuned down a bit - but the result is
a big difference in tone. So, when tuning the F5s in the early 1920s using C=256 as concert pitch, Loar was hearing
something different from what we are hearing today. Hmmmm.
If the subject interests you, I wrote an
in-depth white paper about three years ago entitled What Was Loar Hearing? You might want to read it to get a better
idea of what was going on with tap tuning and concert pitches of the day.
The white paper is free and can be downloaded from the downloads page on our web site (eighth document from the bottom of the
page).
|
Product Highlights
· H5 Mandola Kits - There seems to be a resurgence in
the interest in the mandola. These instruments are tuned A, D, G, C and offer a rich deep tone. After almost two years of
tooling, we announced our H5 mandola kit a little over a year ago and many
happy luthiers have put together wonderful sounding H5 instruments. Like our
F5, F4, and A5 kits, our H5 kit includes all meticulously crafted pre-shaped
parts and the kit is available in three levels of completion. The most complete
kit is our part #720 and is $699.00 plus P&H. (And, as with our other kits,
there are several options available.)
· Body Assembly Fixtures - We provide our mandolin and
mandola kits with the rim and block set disassembled. We prefer the practice of
assembling the rim in a body-assembly fixture to hold the rim in perfect shape
until the soundboard is glued on (then the entire assembly can be removed from
the fixture). To help you with accurate assembly, we manufacture two-piece body
assembly fixtures that feature an adjustable internal spreader. Our fixtures
are made of red oak and are held above the workbench by rubber feet (to ensure
that the fixture secures the rib/rim at its mid point). Body assembly fixtures
are available for the F5/F4 mandolin (part #350, $139.00), A5 mandolin (part
#351, $130.00), and the H5 mandola (part #352, $148.50) plus P&H.
· Peghead Templates - Having trouble getting your peghead
shapes accurate? Our line of peghead templates are laser cut with great
precision. The shapes and peghole locations were derived from original Gibson
instruments (the F5 peghead template in the center of the photo is laying over the
peghead of Lloyd Loar's personal F5 mandolin). These templates help you layout
your pegheads and peghead veneers as well as provide accurate hole spacing and
positioning for the geared machines. We make our templates from luminescent
green acrylic plastic so they can be easily located in your shop. We have a
wide range of templates available, and you can see them all in our web site here.NOTE: Please consult the Shipping & Returns page on our website for a P&H table. |
Luthier's Tip... Scroll Protector
One of the tricky parts of preparing
soundboards and backboards is carving the scrolls. In addition to shaping the
volute properly, the low area of the soundboard and backboard near the scroll
has to be shaped down close to the scroll and this requires forcing your gouges
and chisels in the direction of the scroll. If the chisel slips or exits from
the wood when you didn't expect it to, there is a good chance the chisel will
ding the scroll. When working on the soundboard, where the wood is a bit more
delicate than the maple backboard, if the chisel were to exit with too much
force, and strike the side of the scroll, there is a chance it could crack the
scroll.
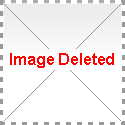
An easy way to protect the scroll from
damage is to place a leather caul in the scroll's opening. The leather caul
will act as both a protector and shock absorber. It will also help protect the
cutting edge of your chisels. As an added feature, you will be able to work
more confidently knowing that you have better control of where your chisel will
end up.
As with any tool, stay focused on where your
hands and fingers are. Unfortunately, inserting a leather caul in the scroll's
cutout doesn't give your free hand any more protection.
| |
Product of the Month: Tap-Tuning Service
We have a very special offer to help you kick off the New Year. For any mandolin or mandola kit order received in the
month of January that also includes our tap tuning service option, we are going
to offer a whopping 50% discount off the tap tuning service - that's an
exceptional $100.00 savings on the tap-tuning service! So, until January 31,
2010, if you enter promo code kit100tap when you order an F5, A5, or H5 kit with
the #900 tap tuning service, you'll get a mega-bonus saving of $100.00! Happy
Tap Tuned New Year!
|
|
|