|
|
|
Dear Luthiers,
We're listening to you!
A few months back, I asked for your thoughts on our web site and specifically wanted to know how important on-line ordering was to you. I received quite a bit of input (thank you!) and the information was very helpful.
Some luthiers said that they really like calling in their orders and having a chance to talk to me directly and ask questions (I make it a point to be available to you - direct communication with you is very important to me). Others said that mailing in an order works just fine; they prefer not to use credit cards. Some requested that we make PayPal available. Several luthiers said that regular email ordering works for them. And, many luthiers said that on-line ordering through the web site would enable them to order things at 2:00 a.m., when then are knee-deep in a project and know they can't get us on the phone at that hour.
We took all of that to heart and have been focusing diligently on the four methods of ordering. Phone orders, orders through the mail, and email orders will continue as they are (and I will always be available to you on the phone). And, I am excited to report that Kali Nowakowski, our marketing manager, has been working with a web developer for the past few months to launch a full e-commerce site for ordering of our parts and services. That program will include the opportunity to use PayPal. At the moment, we do not have a firm launch date for the new site (it's a huge undertaking) but it will be before mid-summer. And, it will include a re-design and updates to the Lloyd Loar and Orville Gibson sections of the site. We'll keep you updated with our progress.
So, your input means a lot to us, and we think of our parts, services, and support as an extension of your needs.
We're listening to you!
Thanks for building with us...
Roger Siminoff
|
|
That elusive "woody sound"
I often have discussions with folks about achieving that "woody sound" when building an instrument, and the conversation typically leads to a discussion of just what that woody sound is. After all, if we can't describe it, how will we know we've got it when we get there?
The human senses are interesting. While they are powerful tools to help us discern what we see, hear, smell, touch, and taste, we are often left with lesser tools to describe what those senses tell us. So it is with sound. Describing the finite qualities of sound is like describing the virtues of a gourmet dinner or a fine wine. It's rather complex, and I often find it fairly difficult to eloquently describe what that woody sound really is.
It seems that it can be best defined by first explaining what it is not. For me, that elusive woody sound is NOT the sound of the strings or of a method of a "chopping" picking technique, but rather the sound of the instrument itself.
It is the overall sound of the soundboard, backboard, and air chamber - as a whole - whose warmth and richness stem from their structure and their tuning. The woody sound is a result of the wood being sensitive enough to respond to the energy sent from the strings. The denser the wood (and, therefore, the heavier the mandolin), the less we hear of the wood and the more prominent the strings become. The less dense the wood (and lighter the mandolin), the more sensitive the wood becomes and the more capable it is of responding to the energy sent from the strings.
Too thick (i.e., heavy) is a bad thing. Too thin (i.e., light) is a bad thing. And somewhere in the middle is that sweet spot - the balance between the strings producing the energy and the body of the instrument producing the sound.
Getting there is the magical combination of building enough instruments to get soundboards and backboards to the correct stiffness, and the sensitivity to listen carefully to the results from changes you make.
It's that secret sauce that luthierie is all about... |
What's New?
· Position Dot Stock Drill Kit - We've just added a wonderful tool to our tools price list. This hand/twist drill facilitates the drilling of side position dot stock into the binding. Rather than drilling holes into your binding - and burning it - this hand-held tool is twisted into the binding for a clean, precise hole. The support is fitted with a .076˝ drill bit to provide for an interference fit of the accompanying .078˝ position dot stock. Enough dot stock for 3-5 instruments. Part #855 is $11.95 plus $7.50 P&H.
· Ebony Fretboard Extenders - A lesser-known feature of the original F5 mandolins is that they had ebony fretboard extenders. While most builders use maple extenders today, the ebony extenders added additional mass and stiffness to the end of the fretboard. The ebony extender inhibits damping and promotes sustain. We've been producing them for a few years, and it looks like more and more folks are beginning to use them. Part #338-A is $44.00 plus $7.50 P&H.
· Mandola Block Sets - We continue to add mandola components to our price list. Our latest is this H5 block set shaped from Honduras mahogany. The set includes a headblock, tailblock, corner blocks (2), and a maple cap. Part #310-B is $28.50 and the P&H is $7.50 |
Luthier's Tip: Flush trimming soundboards and backboards
In The Ultimate Bluegrass Mandolin Construction Manual, I showed a somewhat simple way to flush trim soundboards and backboard to the rim (Fig. 10.10, page 91). That method suggested sanding the plates flush to the ribs, and it was intended for one-time builders who were not planning on tooling up to build several instruments.
A more advanced and faster method beyond the sanding technique is to do it with a router. Here's what you need:
1) Prepare a fixture with a cutout that is the same shape as the F5 body, but is ¼" SMALLER all around. This smaller opening will allow the mandolin soundboard's binding edge to rest on the ¼" lip of the fixture and provide an opening for the belly of the soundboard to protrude below. Then, as shown in the accompanying photo, prepare several small pieces of plywood shaped to fit around the rim of the opening, to hold the rib in place. With this set up, the assembled body can rest in the fixture, parallel to the work surface, with the crown of the soundboard protruding unobstructed into the opening below.
2) Set up a router with a flush-bearing bit on a support arm over a flat work surface.
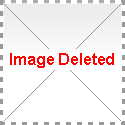
Then simply work the body into the router. Be sure to consider the rotation of the cutter and the direction of the cut when working both with and against the grain, and work slowly so that you don't chip up the edge. And, as with all machines tools, keep your hands clear! | |
Product of the Month: Tuning Machines
For the month of March, 2008, you can take advantage of an offer to purchase a set of our F5 mandolin machines and save $10.00! These machines are made for us by Gotoh and feature a unique post bushing system (hidden in the peghead) that is comprised of Delrin® bearings with spring-steel washers that ensure smooth turning. Standard 29/32˝ post-to-post spacing with simulated MOP plastic buttons standard. (We have numerous natural buttons that are made to fit these shafts, which can be purchased separately). Includes mounting screws and eyelet-style bushings. Part #301-G (gold) are regularly $64.50 or #301-N are regularly $61.50 - during March you can deduct $10.00 from either set! Limit one set per customer. P&H is $9.50. |
|
|