|
|
Tap Tuning - is it necessary?
In the last year since The Art of Tap Tuning was launched, we - and others - have seen a marked rise in the interest of tap tuning. More people are trying it, more people are having success with it, some of the nay-sayers are saying "maybe," and several major manufacturers are beginning to think about including tap tuning in their production with the hope of achieving a greater consistency. Even equipment manufacturers are raising eyebrows on what tap tuning might mean to them (but more on that in a moment).
One question that often pops up from folks who buy parts and kits from us is, "Do I need to tap tune?" Tap tuning is absolutely not necessary. You can put a mandolin together, not tune anything, make the tone bars like the drawings, make the soundboard and backboard like the drawings, glue it up, spray it up, string it up, and you'll have a mandolin that sounds good.
Or, you can study tap tuning, get a grip on the technique, and be equipped to adjust the structure of your instrument so that it sounds great. Tap tuning also gives you consistency, and it lets you know something about the parts of your instrument that you can't learn any other way.
Okay, let me get off the soap box and back to the interest from manufacturers. The strobetuner folks have seen a shift in interest towards tap tuning. One of the companies I work closely with is Peterson Electro Musical. They take tuning seriously, and tap tuning is now a part of that picture. In fact, they take it so seriously that the new version of StroboSoft® that just released a few days ago has a new built-in tap tuning function that locks onto a note when you tap and holds it on the display until you tap again. This means that with StroboSoft v2, you don't need a separate compressor. And, there are thresholds you can set to establish the high and low range of the tapped sound StroboSoft measures.
So, I'm happy to report that tap tuning doesn't appear to be a fad. And, I think each of you who have been working with tap tuning should take a bow; you are fanning the fire of this technology, and I believe that musicians in the years to come will be grateful for your efforts.
| |
Dear Luthiers,
Behind the scenes.
Of the many things important to our business, only three facets are really visible to you: our customer service communications, the quality of our parts, and the speed by which we provide these to you.
Behind the scenes there is a lot going on that you can't see. One of key invisible things is how we select and deal with our vendors; the folks we buy raw materials, parts, and production supplies from. These relationships are equally important to us, and we take them seriously, honestly, and respectfully.
Our vendors are served by an association called NAMM: the National Association of Music Merchants. Each year, NAMM hosts two conventions, one on the West Coast (called the "Winter NAMM") and one in the mid-states during the summer. I've been attending NAMM conventions for more than 40 years (only a small part of NAMM's 100+ years of existence), somewhat irregularly when I first began making banjo parts in the 1960s, and then on a very regular basis beginning in 1973 when we launched Pickin' Magazine. For many years I was on the NAMM Advisory Board and have had the opportunity to lecture on industry-related topics at several conventions. Many of the exhibitors were my first advertisers. We watched each others' businesses grow, and we watched each others' families grow. And often when I go to a show, I'm not only meeting with my good friends, but with their sons and daughters who are following in their parent's footsteps. Needless to say, NAMM is more than just a trade show for me - it's a family reunion.
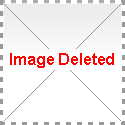
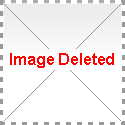
This year's "Winter NAMM" was held at the Anaheim Convention Center consisting of four huge buildings plus a lower level exhibit hall. More than 1,500 exhibitors showed their latest and greatest products to approximately 88,000 attendees over the four days of January 17-20. (You have to be in the music business as well as a NAMM member to get in.)
Our team went to the show where we met with tone-wood suppliers, the folks from Gotoh, Hal Leonard (yes, another book to come), Behringer, Peterson, and too many more to mention here. We spoke to several manufacturers about their interest in tap tuning. And, of course, we paid special attention to new products and trends.
Sorry if you called our office and we weren't in on those days, but we were keeping abreast of things to provide you with the very best possible service and products.
Thanks for building with us...
Roger Siminoff
|
|
What's New?
· Mandola Necks - Our tooling took awhile, but we're now up to speed on pattern carving mandola necks. We can carve them from curly maple, regular maple, and mahogany. (Or, we can carve your wood if you prefer.) Our profile is patterned after the H5 and the neck comes with ears attached. Truss rod installation and peghead shaping is an optional service. Our curly maple mandola necks are #1322 and are $105.00 each plus $13.50 P&H.
· The Physics of Music - At long last, The Physics of Music notebook will be ready to ship in the first week of February. This is a student's notebook from Professor Loar's last class at Northwestern University (during the summer of 1943) complete with reproductions of the original illustrations. I have added notes in the margins to clarify and expand on several points. Great stuff about musical acoustics and how string instruments produce sound. The notebook is our part #508, $24.95 each, plus $7.50 P&H.
· W/B/W Side Binding - We're happy to announce a wonderful addition to our selection of bindings. We now carry .040" thick ivoroid/black/ivoroid celluloid binding with the black stripe on the side just as used on some of the original F5 mandolins. (As of January 1, 2008, a piece of this binding is standard in our F5 #700 and A5 #710 mandolin kits for side binding of the fretboard.) Fretboard side binding #409 is 3/16" x .040" x 26" and $9.75 per length. P&H is dependent on the number of pieces ordered. |
Luthier's Tip: Installing Rosettes
We're getting more and more folks interested in building F4s from our kits. And as this interest increases, we get more questions about how to inlay the soundhole rosette. It's difficult for us to prepare this notch by machine routing because the soundboard needs to be brought to the first level of sanding before the notch can be cut. Once the soundboard is rough sanded, the rosette's notch is actually fairly easy to cut.
To begin, place the fretboard on the elevated portion of the soundboard, and lightly mark the soundboard where the binding edge of the fretboard will fall. This line will indicate where the rosette must come up to and where it will end under the fretboard.
Then, use three or four pieces of painter's blue masking tape (it doesn't tend to lift the wood's grain as readily as regular masking tape) and tape the rosette in place. Double check the positioning of the rosette. Then, removing one piece of tape at a time, scribe along the edge of the rosette carefully with an X-Acto® knife fitted with a #11 blade, and replace the tape as you work the next section. Make sure to keep the blade vertical so that you trace the true width and shape of the rosette. This will give you a very fine line around the inside and outside of the rosette. When you have outlined the entire rosette, remove all the tape and the rosette, and carefully cut the inside and outside lines to a depth that will accommodate the thickness of the rosette. Then, using a small sharp chisel or X-Acto blade, remove the wood from between the cuts. Go only as deep as necessary so that the trough you make corresponds to the thickness of the rosette. The key to doing a good job is to work in very good lighting, be seated and comfortable, and take your time. Cut the ends of the rosette so that only ¼" or so continues under the fretboard. Once the rosette is glued in place, sand the ends of the rosette (that are under the fretboard) flush to the fretboard plane of the soundboard so the fretboard fits properly. | |
Product of the Month: Carving Service - Customer Stock
For the month of February, 2008, you can take advantage of an offer to have us carve your backboard and/or soundboard wood at a special savings. Our unique pattern carver has been producing high-quality boards for luthiers around the world for more than 40 years. Our carving service includes profiling the boards around their outer edges - including the cut into the body scroll - to the precise F5 shape (or we can leave them oversize if you prefer). February's special price is $50.00 per board (save $10.00!). One board or set of boards (backboard and soundboard) per customer for the month of February 2008; A5, F5, or F4; photo shows optional f-hole service; email or call for free wood-preparation drawings and instructions. |
|
|