|
|

Although I never forget or take for granted the value of the relationships I have, Thanksgiving is a special reminder of how important my friends and business associates are. I enjoy my communications with you, truly value your friendship, and greatly appreciate your business.
The Holiday season is upon us and the coming of a new year is just around the corner. All of us here wish you and your family happiness, good health, prosperity, and peace. May the New Year bring you all the good things you hope for.
Roger | |
Dear Luthiers,
For many years, I have had in my collection of Loar memorabilia a student's lab notebook from Professor Loar's last class when he was teaching at Northwestern University in Evanston, Illinois. About six months ago, I finally began reading it cover-to-cover and was delighted by what I found. In addition to a basic class on musical acoustics, Loar talks about the importance of tuned bodies and air chambers, and I was tickled to read his thoughts on why "lute family" instruments (mandolins, guitars, etc.) are incapable of producing quality musical tones. Hmmm. As I read through the text, I felt that I was sitting in class with Professor Loar. It's outstanding! Aside from some revelations I had from reading the book, I was motivated to make the content available to my fellow luthiers and give you a chance to attend a class with Lloyd Loar, too. I've transcribed the handwritten text verbatim to preserve the grammar, language, and spellings of the day, and I included scans of the numerous original illustrations so there would be as little deviation as possible of what Professor Loar drew on the chalk board. When necessary, I've provided clarification, examples, and additional information as sidebars. In about two months, I'll be announcing the release of this publication. Because of the short-run nature of the text, it will only be available from us directly (not through Hal Leonard or luthierie shops as with my other books). If you're interested in Lloyd Loar's work and want to know more about his thoughts on musical acoustics, you'll enjoy this text. Please send me an email at siminoff@siminoff.net if you'd like to be on the announcement list.
Thanks for building with us...
Roger Siminoff |
|
De-damping - what is it about?
In my very first mandolin book (Constructing a Bluegrass Mandolin, 1973), I wrote about the advantage of placing a new string musical instrument in front of a speaker cabinet to break it in. In the nearly 35 years that have passed, I have continued to experiment with the break-in process using various means to excite the backboard and soundboard of an instrument with the goal of accelerating its aging process to enrich the instrument's tone.
Along the way, it became clear that the physical aging of the wood - a process called polymerization - could not readily be accelerated, at least not by the means at my disposal. However, the continuous movement of the wood, especially over a sustained period of time, improved its flexiblity; one attribute of aged wood (the other attribute being brittleness).
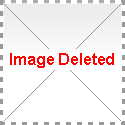 This prompted me to embark on building some unique systems to excite the instrument's air chamber. These included, but were not limited to a mechanical strumming machine, a vibrating motor (an idea I borrowed from German scientist Gottfried Lehmann), and external excitation of specific frequencies from a uni-directional, high-intensity speaker.
I'd like to say that the process is unique and that I am the inventor. But the truth is that this technique (which they refer to as "de-damping") has been in use for many years by the European viol-family luthiers and repair folks. The name is derived from the idea that the technique would set up the wood to produce tone and not damp it.
Comments and questions about de-damping abound and many have found their way to the chat sites. Some folks write about the great results they have experienced with instruments we have de-damped. Others ask how and why this works, while others respond that you should "just play the heck out of it yourself." Well, playing the "heck out of it" will certainly warm it up, but I don't know any musician who can sit in one place and play a D chord (or whatever the resonant frequency is of the air chamber) for 24 hours straight! The repetitive working of the soundboard and backboard from the de-damping process does a lot more to stress-flex the wood than minutes or hours of playing.
In our website, I'm glad to share how you can set up a strumming maching to do the de-damping yourself, see here. The electronic systems for generating sweep frequencies are a bit more complex - and more expensive - so I don't include those on my website. Click here if you'd like to read some testimonials and learn more about our de-damping service. |
What's New?
ˇ Nut and Saddle Files - We have always supported the idea of using V-shaped files for cutting the string notches in nuts and saddles. In the V-slot, the string is solidly anchored against two contact points, and you can change string gauges with ease - something you can't do with gauged-files (files that cut a notch the same size as the strings). We located a great V-shaped file that will withstand the cutting of pearl, abalone, and bone nuts as well as the notches in a wooden bridge saddle. Our part number is #450, each file is $5.95 and the P&H is $6.00.
ˇ Pearl Nuts - This is a part we should have added years ago, but better late than never! These solid mother-of-pearl nut blanks are similar to the pearl nuts used on the original F5 instruments. Pearl is harder than bone and provides a more rigid support on which strings can vibrate. The hardness of pearl enhances the treble qualities and generally improves tonal clarity. Our pearl nuts are part #024, and cost $10.00 each.The P&H is $6.00
ˇ Mandola Body Fixture - We're happy to announce our new body assembly fixture for the H5 mandola. As with our F5/F4 and A5 fixtures, this assembly fixture is made of red oak with an adjustable center expander section. The black knobs allow the fixture to be easily split open when the rim/soundboard assembly is ready for removal from the fixture. Rubber feet keep the fixture above the workspace and centered on the rim. The H5 assembly fixture is part #352, $143.50 and the P&H is $15.75. |
Luthier's Tip: Save your ribs!
I've heard from many folks about their problems bending ribs over heated pipes, especially the rib piece that goes between the two points. Some luthiers have mentioned how many pieces they have cracked before they get a good one. Not all cracked ribs are useless. If a rib cracks somewhere along its inside surface (and that's where most of the tight bends cause cracks to occur), you can often save the piece by gluing the crack closed with cyanoacrylate glue ("Crazy GlueŽ"). Except for the one tight curve in the waist of the long bass-side rib piece, the cracks usually occur in a place where the rib will be glued to an internal block piece, so the glued seam will be invisible and well secured. To glue them closed easily, prepare a male and female clamping caul set from some scrap maple. Cut the curve to match the final shape of the rim and be sure to make the inside curve more acute than the outside curve to allow room for the rib to be clamped between the two halves. Cut a piece of wax paper about 4" x 4". Then, put a liberal amount of cyanoacrylate glue on the cracked rib section, cover it with the wax paper, and clamp the rib and wax paper tightly between the cauls. Allow about an hour to let them dry. Remove the cauls, peel away the wax paper, sand away any residual glue, and you'll be good as new! | |
Product of the Month: Gift Certificate
As we near the Holidays, it's time to begin thinking about gift giving ideas, and we think we have the perfect gift. From November 25 to December 25 only, we are offering a special 10% discount on our gift certificates (the certificate may be used any time, but the discounted offer is only valid if purchased between 11/25/07 and 12/25/07). They can be made out for any amount, but you pay 10% less than the face value of the certificate. To have it arrive in time for Christmas please call us no later than December 17th. |
|
|