|
|
|
Building your dream...
We get customers calling from time to time telling us how they'd like to build their dream mandolin, but can't find the wood they want. Often, we respond, "we've got some of that Claro (or whatever) you're looking for!" We regularly visit a lot of wood sources and occasionally come across unusual and special woods that we can't resist, but the quantities are so small and the opportunities are so sporadic that we can't include them in our regular price list. So, if you're dreaming of something special, please don't hesitate to call us and share your dream - there's a possibility that we can help make it a reality for you.
Thanks for building with us...
Roger |
|
To "kit" or not to "kit," that is the question.
There's been a lot of chatter on the forums - and we receive a lot of emails - about the virtues of building from a "kit." Things like: "You should build from scratch before building from a kit"; "Is someone who builds a kit really a luthier?"; and "Professional luthiers don't build from kits." Interesting subject and it leads to a lot of conjecture. To begin with, we've never really liked the word "kit" - it conjures up images of a box of snap-together plastic parts to make a kid's model airplane (not that there's anything wrong with that!). However, until we find a better word, "kit" does, as Webster's states, describe a set of parts to be assembled. Then, it is interesting to note that most major manufacturers of mandolins don't have their builders individually carve soundboards, bend rims, shape necks, and so on. The builders work from a set ("kit") of parts ready to construct. In fact, the builders of the much heralded Loar-signed Gibson F5 mandolins assembled their instruments from a bunch of shaped parts that came from other folks in the plant. And this practice continues to today. In the early '70s I took this photo of a whole bin of Gibson F5 necks already shaped, with truss rod and scroll strengthener installed, just waiting as one component of the "kit" the builders were selecting parts from. In my mind, you can do the heavy carving if that's important to you, but I have just as much respect for luthiers who let us do the initial work with one of our kits so they can focus on building and finishing a fine instrument. Of course, building from scratch provides excellent insight to what goes into building the instrument from the ground up (and that's why I wrote two books about it). But, to set the record straight, I don't shun folks who build from a kit. I equate it to a contractor who builds a fine house but doesn't make his own doors, bricks, shingles, windows, and so on. He's not less of a contractor building from that "kit" than you would be less of a luithier building from a mandolin kit. Just food for thought... PS: If you have another word for "kit," we're all ears siminoff@siminoff.net
|
What's New?
· Template and Fixture Drawings - New to our family of ProSeries Drawings is a set of plans for preparing the templates and fixtures necessary to building an F5 mandolin. The set consists of 14 full-size fixture drawings that includes; peghead shaping, truss rod slotting, tone bar gluing, body assembly, dovetail joint cutting, V-joint cutting, fretboard binding bending, and several templates. The Drawing set is part #DTF5 and is $24.95 plus $8.00 P&H.
· Mandola Bridges - About four months ago, we began to make replica bridges for the H5 mandola. These bridges are made of Gaboon ebony with either nickel or gold hardware. Each bridge comes with instructions for cutting the strings notches (so you can match them to your particular preference) and fitting the bridge to the soundboard. The part numbers are 308-MN for nickel ($42.00) and 308-MG for gold ($44.00) plus $6.00 P&H.
· Decorative Buttons - We have a wonderful collection of decorative buttons for our mandolin machines. These include antiqued pearlized plastic (2), grained celluloid (3), abalone (4), black buffalo horn (5), figured mother-of-pearl (6), white snail (7), figured snail (8), and white bone (9). For comparison, the button on the left is the standard pearlized plastic button (1) that comes with our machines. Please click here for more information and individual prices. |
Luthier's Tip: Dust-free work
Almost every procedure in our shop makes sawdust. About 80% of it gets taken away by an overhead dust collection system, but some of it just sits there on the work, blocks our view, and waits to be blown away (which is hard to do with a dust mask on). To keep the work clean and to 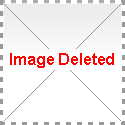 make it easier to follow lines, blow chips away from drills, and keep drill bits cool, we use small air hoses. These attach to our air lines with regular snap-fittings, have a small shut off valve to allow adjustment of the air volume, and step from a large hose down to a small hose that terminates in a piece of thin brass tubing to direct air flow. The hose can be attached to Dremel tools and directed towards the bit when routing for inlays or clamped to drill presses and other tools. Of course, it's still a good idea to wear a dust mask.
| |
Product of the Month: F5 Machines
October's product of the month is our #301-N (nickel) or #301-G (gold) mandolin machines. Made for us by Gotoh, these machines are excellent 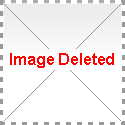 replicas of the machines used on the original F5 mandolins and feature peaned supports for the worm gear, an embossed backstrap, and a 14:1 gear ratio. The #301-N is regularly $61.50 and the #301-G is $64.50. See the coupon below for special "Product of the Month" savings. |
|
|