Greetings!
Michael Cowley, CPMM October's Month's Tip:
Work Order Planning - How Many Details do You Need? |
Measure Your Maintenance Performance... Are You Making a Difference?
For this month's topic we will talk about measuring the performance of your maintenance organization. Over the years I have taught many classes and written a few magazine articles on this topic. I will do my best to condense the information so it will fit in the space Anne allows in the news letter.
If you would like more information after reading this contact Anne and she will send you a copy of my white paper on this topic. It will provide you more detail and information on the whole measurement and scorecard topic.
There are hundreds of possible measurements for the average maintenance organization but I, as most of you know, will keep it simple especially for the newsletter. One very important thing to keep in mind before we get into the details of performance measurements is the prerequisites. In order for any measurement program to be meaningful you must first have accurate data. You must have a completely install, well-maintained, and disciplined work order management system (CMMS). And, you must populate it with well-documented work orders for all work.
Below I have listed the most common measurements for most organizations and maintenance teams. You will notice I normally do not talk too much about $$ per square foot. The reason is that to accomplish the square foot unit cost data you must have the measurements I have listed below. The per square foot measurements are very easy to calculate once you have mastered the others.
Classic Measurements
- Back Log- Measured in backlog weeks. It is a measurement of the amount of work waiting to be completed. It's not emergent work but just things on your to do list. Sorted by location, asset, craft, crew, etc. The goal for most organizations is 4-6 weeks.
- Work Distribution - Measured several ways; man-hours, manpower, or percent of total hours available. This measurement tells you where you historically used your man-power or resources. No goal for this measurement just information.
- Reactive Work - Measured in man-hours or a percent of total man-hours available. This measurement tells you how much of your work had some element of chaos associated with it. Remember, reactive work is 4-6 times more expensive as planned and scheduled work. Goal is less than 20% of total maintenance man-hours.
- Preventive Maintenance (PM)- Measured in percent of man-hours performed on all types of PM work. This is a great indicator of where your organization is on its path as it heads away from chaos to world class maintenance. Goal is approximately 50%.
- Late Preventive Maintenance - Measured in numbers of late PM work orders based on the scheduled due date or the PM. If you are serious about asset reliability and improvement, late PM's must be less than 2%. Goal is a late PM is one that is completed within 10% of the PM frequency.
- Planned Work - Measured in percent of total man-hours that are spent on work that has some level of planning. This is also a good measure to see if you are heading in the right direction as it relates to proactive work. Goal should be approximately 80% of total work completed.
- Scheduled Work- Measure this right after you have planned some work. Now put it into a weekly work schedule. The schedule process causes the team to think and discuss the upcoming work which will improve efficiency, quality, and lower costs. Goal should be 50-60% of all man-hours completed each week.
- Total Asset Maintenance Costs - Measured in dollars per-year per-asset. A great measurement that will let you know when you are spending too much on an asset as compared to its estimated replacement value. Note: Don't forget to include your contractor costs for that asset also. Goals and objectives of your organization can be explained by talking to your financial officer. They will talk you through the calculations.
So this is the 'KISS' principle explanation of measuring your maintenance performance. Call or email us if you would like to discuss, or any topic, in more detail.
Good Luck and See you Next Month!
|
|
What Do You Want Us to Talk About ?
|
It is time to hear from you and what topic(s), issues, or questions you would like to have us cover in the Tip of the Month.
|
If you are planning to attend, I hope you will sit in my programs and visit our booth. Look forward to seeing you there!
NFMT
October 2-3, 2012
IFMA
Oct. 31 - Nov. 2, 2012
March 12-14, 2013
Baltimore, MD
|
60 FREE Minutes with Mike
|
- Pressing Maintenance Management Issues?
- Problems/Dilemmas?
- Advice and Solutions?
- Future Long-Range Plans?
- Anything at all...
Let's arrange a Free 60-minute conference call with Mike. No strings attached and no sales pitch just answers and solutions to your issues.
|
If you would like to contact them, please click on their name.
Director of Maintenance Systems
Director of Marketing and Education
|
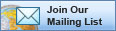 |
Join Our Maintenance Community |
|
|